Use and Selection Guide
Fall Protection
Contents
- 1 PURPOSE AND SCOPE
- 2 DEVELOPING A CORPORATE PROGRAM FOR SAFETY AT HEIGHT
- 3 COMPONENTS OF A PERSONAL FALL ARREST SYSTEM
- 4 SELECTION OF PERSONAL FALL PROTECTION EQUIPMENT
- 5 PLANNING THE USE OF SYSTEMS
- 6 INSPECTION OF FALL PROTECTION EQUIPMENT
- 7 CLEANING, MAINTENANCE, AND STORAGE
- 8 DEFINITIONS
- 9 REGULATIONS AND STANDARDS
- 10 ISEA FALL PROTECTION MANUFACTURERS
- 11 FOR MORE INFORMATION
Contents
- 1 PURPOSE AND SCOPE
- 2 DEVELOPING A CORPORATE PROGRAM FOR SAFETY AT HEIGHT
- 3 COMPONENTS OF A PERSONAL FALL ARREST SYSTEM
- 4 SELECTION OF PERSONAL FALL PROTECTION EQUIPMENT
- 5 PLANNING THE USE OF SYSTEMS
- 6 INSPECTION OF FALL PROTECTION EQUIPMENT
- 7 CLEANING, MAINTENANCE, AND STORAGE
- 8 DEFINITIONS
- 9 REGULATIONS AND STANDARDS
- 10 ISEA FALL PROTECTION MANUFACTURERS
- 11 FOR MORE INFORMATION
Foreword
Workers are exposed to fall hazards in almost every single industry. The U.S. Bureau of Labor Statistics reports 700 fatal falls to a lower level in 2022. These falls continue to be the leading cause of construction worker deaths. According to Liberty Mutual’s 2023 Workplace Safety Index, falls to a lower level are the third leading cause of disabling occupational injuries, costing businesses $6.09 billion a year.
When properly designed, implemented, and executed, a comprehensive fall protection program is the best course of action to protect workers and prevent these unnecessary injuries and fatalities. Fall hazard elimination, fall prevention, and personal fall protection equipment are the key elements of a fall protection program.
The first element to consider once a fall hazard has been identified is fall hazard elimination, or “engineering out the hazard.” This process consists of redesigning the working environment, work processes, or work procedures. If eliminating the fall hazard is not possible, fall prevention should be considered next.
Passive fall protection can be accomplished in several ways: scaffolds, guardrails, walls, covers, barriers, and movable platforms may be constructed to provide a barrier between the worker and the fall hazard. If both fall hazard elimination and prevention are nonviable options, personal fall protection equipment must be used.
Personal fall protection equipment is available in a plethora of options for all jobsites and applications. Full body harnesses, lanyards, and retractable lifelines are most common. Occupational health and safety regulators require personal fall protection for workers at various height levels depending on the job.
The Fall Protection Product Group at the International Safety Equipment Association (ISEA) has prepared this User Guide to provide practical, hands-on guidance for fall protection users and administrators. Selection, use, maintenance, and inspection of fall protection equipment is covered in this User Guide. The information is based on OSHA regulations and national consensus standards in North America pertaining to fall protection. While the guide does not attempt to describe fall protection globally, links to information on fall protection regulations and standards around the world are included.
The guide is available online on ISEA’s website: safetyequipment.org. It may be accessed online or downloaded without charge. The guide will be updated periodically, with the effective date shown on this page. If the guide is downloaded, check back periodically to ensure the latest edition is being used.
Additionally, the user should contact the manufacturer of the specific fall protection equipment being used in the workplace for current manuals and product information.
Purpose and Scope
Purpose
The purpose of this Use and Selection Guide is to:
- Provide guidance for fall protection planning to either remove the fall hazard, prevent access to the fall hazard, restrict worker movement at the fall hazard, or provide the proper fall arrest equipment.
- Illustrate fall protection systems.
- Familiarize fall protection equipment users with the appropriate occupational health and safety laws and standards pertaining to their use.
- Assist in the proper selection, care, use, and inspection of fall protection equipment.
For specific applications, users should always consult the individual manufacturer’s guidelines.
Scope
These guidelines are written for all personal fall protection equipment users– anyone responsible for managing an employer’s fall protection program, supervising employees, conducting training, or inspecting equipment. Everyone involved needs to be knowledgeable about fall protection.
- Section 2 provides an overview of a fall protection program.
- Section 3 describes the components of an active fall protection system.
- Section 4 lists typical components for various work scenarios and applications.
- Section 5 provides guidelines for planning the use of active fall protection systems.
- Section 6 details how to inspect the components of an active fall protection system.
- Section 7 gives guidelines for cleaning, maintenance, and storage.
- Section 8 contains definitions for terms used in fall protection.
- Section 9 provides a list and links to OSHA and consensus standards.
- Section 10 lists the members of the ISEA Fall Protection Product Group.
- Section 11 contains links to additional sources of information on fall protection standards and regulations.
Developing a Corporate Program for Safety at Height
How do I get started?
The most effective Fall Protection Program (FPP) begins with the employer. Employers must identify and understand fall hazards to develop a comprehensive FPP with their workers. Once all fall hazards are understood, the program’s purpose is to eliminate fall hazards or provide appropriate protection against them. Control method(s), equipment needed, and training requirements will be identified in the Fall Protection Program for employees to utilize their equipment according to its specific manufacturer’s instructions.
The following is an example flow chart of a Fall Protection Program.
Understanding Regulations and Standards
The Occupational Safety and Health Administration (OSHA) provides fall protection regulations for general industry, construction, maritime, and several other industries. In Section 9 of the OSH Act of 1970, the law states it is the employer’s duty to provide their workers with a workplace environment free from recognized safety and health hazards– fall hazards being one of them.
Employers should obtain copies of the OSHA regulations that apply to their work activities and create and maintain a fall protection regulations file. See Section 9 of this User Guide for a list of OSHA regulations on fall protection. There may also be fall protection regulations that are unique to certain states or municipalities. It is the employer’s responsibility to know and understand the applicable regulations.
In addition to government regulations, there are voluntary consensus standards that address fall protection equipment and practices. American National Standards Institute (ANSI) and the Canadian Standards Association (CSA), in partnership with standards development organizations like ISEA, facilitate and coordinate voluntary consensus standards that specify product performance and testing criteria for personal fall arrest equipment. Unlike OSHA regulations, these standards are not enforceable by law. However, it is important to understand that OSHA may utilize ANSI guidance to enforce their regulations. Relevant ANSI and CSA standards are listed in Section 9 of this User Guide.
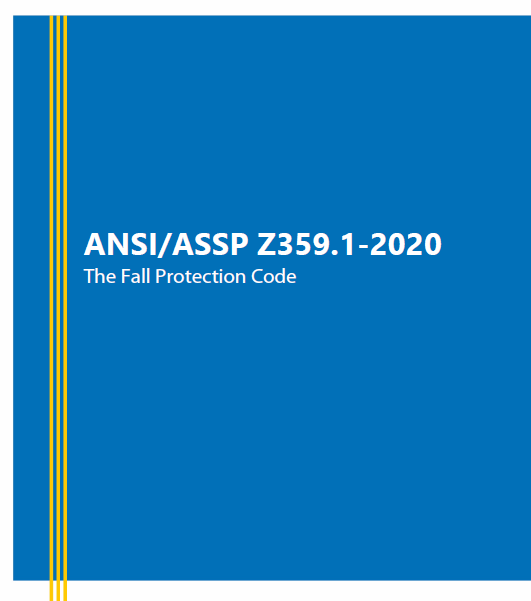
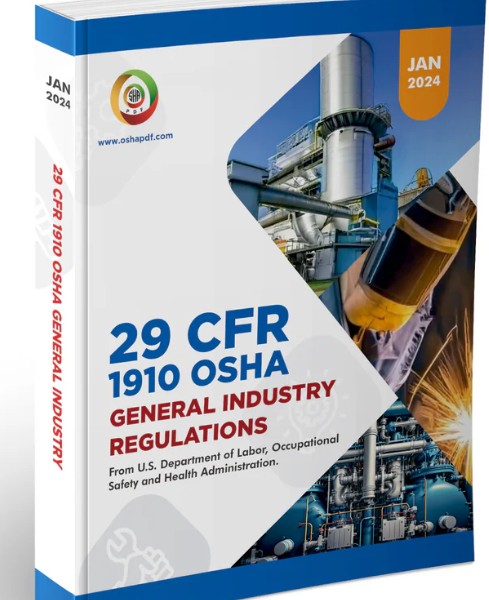
Hazard Identification
Federal, state, and municipality regulations have certain conditions where fall protection is required. A well-conceived Fall Protection Program beings with identifying all hazards in the workplace. Two methodologies for employers to utilize are Job Safety Analysis (JSA) and Job Hazard Analysis (JHA). JSA focuses on identifying and preventing potential hazards for specific job tasks. JHA analyzes the risk, likelihood, and severity that potential hazards pose.
Fall protection is always required when a person is working above anything imminently dangerous like impalement objects, conveyers, augers, galvanizing tanks, etc. In other environments, an employer’s fall protection requirements are usually expressed by a minimum height measurement connected to the work being performed. For example, in general industry applications for walking/working surfaces, the employer is required to provide fall protection equipment any time a worker is at a height greater than 4 feet (1.2 m). In most construction activities, fall protection is required when a worker is at a height greater than 6 feet (1.8 m). Since the height at which fall protection is required changes by jurisdiction and task, refer to your company’s policy to ensure you are following the correct requirements.
The key element to a FPP is identifying and understanding all the physical locations where a fall hazard exists. Where a fall hazard exists, there are two acceptable options: eliminate the hazard or provide protection against it. Many hazards can be eliminated when properly assessed. Changing work procedures, redesigning the working environment, purchasing different materials or products, installing guardrails, or using passive fall protection can often eliminate or prevent the fall hazard. When elimination or use of passive protection methods is not possible, use of active personal fall protection may be required. These harness-based systems can either provide fall arrest devices that allow the worker to reach the fall hazard but catches them if a fall occurs, or restraint mechanisms to keep the worker from reaching the fall hazard altogether.
OSHA 1910.28 and ANSI/ISEA 121-2023 also require employers to be aware of, and prevent, potential dropped objects in the workplace. Falling objects from at-height work applications kill and injure workers each year. Protective equipment (safety helmets and hard hats), preventative equipment (netting and toe boards), and active controls (anchor attachments, tool attachments, tool tethers, and containers) should be taken into consideration.
Fall Protection Program
A site-specific program should be developed after hazard identification. This program details: equipment used, before and after use inspection, work procedures, training for employees before the work begins, fall prevention and protection measures to be used, and how they are to be used, a rescue plan, who is responsible for overall supervision and training.
The program should cover these basic elements and be clearly conveyed and understood by all participants.
Product Selection
A large variety of equipment from several reputable equipment manufacturers is available to employers. See Section 10 of this User Guide for a list of ISEA fall protection equipment manufacturers. The employer can source from thousands of fall protection products to decide which would be most suitable for their specific workplace, their workers, and the hazards they may face. Section 4 of this User Guide provides guidelines for product selection. If the employer is thorough in the hazard identification process, they will be able to determine the type of equipment needed (lanyards, self-retracting lifelines, horizontal lifelines, etc.), features the equipment will need (arc flash, high heat, tie-back, number of harness D-rings, etc.), amount of equipment needed, and where to store the equipment. Once products are selected, training the users and supervisors can take form within the program. Users must understand the differences in product functions and how their fall protection products operate to ensure maximum safety.
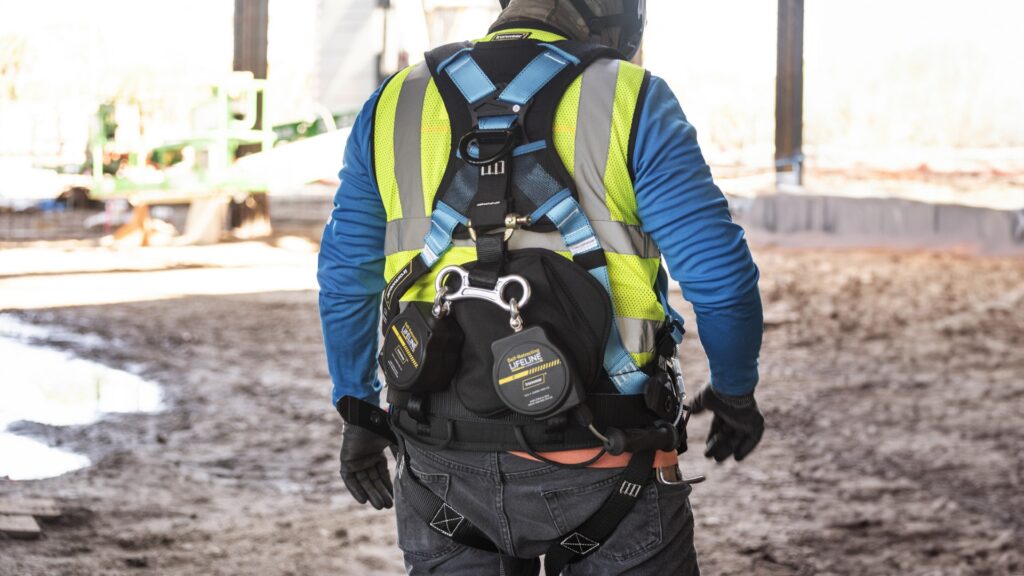
Training
All workers must have experience-based, understandable, and hands-on training before using any fall protection products. Training is an essential step to verify the user has basic equipment knowledge and skill and understands the capabilities and limitations of their personal protective equipment (PPE). Therefore, language barriers must be taken into consideration. Training should be conducted as an initial introduction and repeated periodically for review, validation, and updates as products, policies, and regulations evolve. The training offered must be specific to the site and equipment being utilized and may need to cover more topics than are listed here.
An employer has several options with the FPP to administer their training. For instance, training can be implemented: as part of a new hire process, as employee professional development, through toolbox talks, with safety meetings, as monthly briefings, with annual training courses.
Regardless of the format the training is delivered, it should include all fall hazards and equipment an employee will encounter, including experiential exercises and documents. The hazard identification process will reveal the necessary content for training.
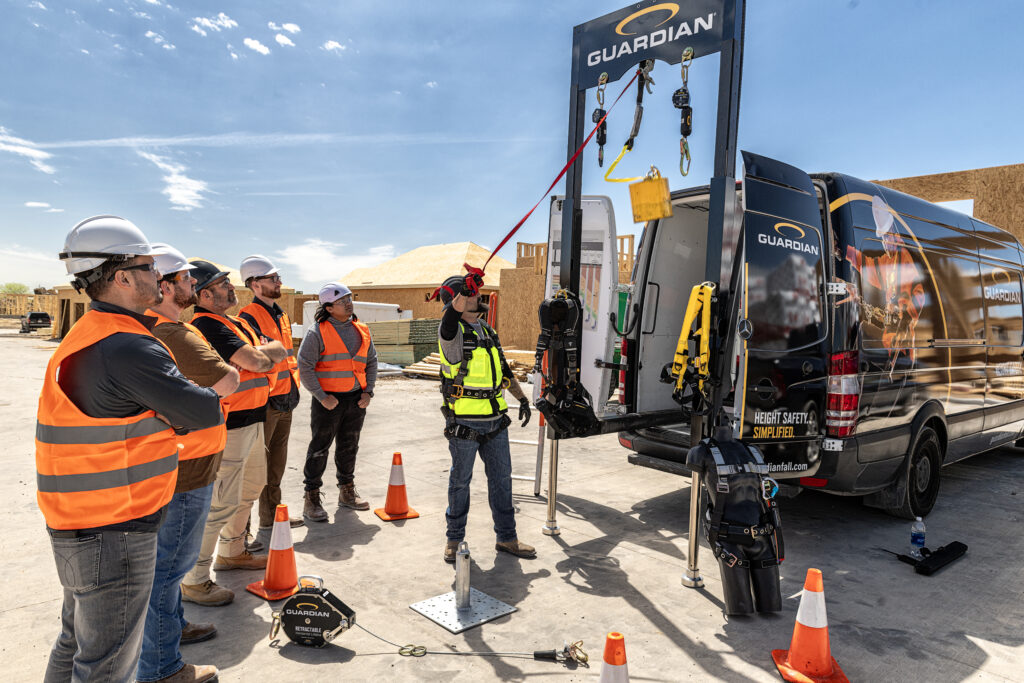
OSHA regulations detail training requirements in 29 CFR 1910.30 for general industry and 29 CFR 1926.503 for construction. State and other jurisdiction standards are similar. Generally, each require that employees be trained in the:
- Identification of potential fall hazards and procedures to minimize fall hazards.
- Correct procedures for installing, inspecting, operating, maintaining, and disassembling personal fall protection systems.
- Correct use of personal fall protection systems and equipment being used, including proper hook-up, anchoring, and tie-off techniques.
- Proper care, inspection, storage, and use of equipment in accordance with manufacturer’s instructions.
Employee(s) must be retrained if there are safety incidents, changes in the workplace or types of fall protection systems/ equipment being used, or if a work performance indicates a lack of understanding and skill necessary to work safely.
Training objectives should educate employees on how to:
- Recognize fall hazards and eliminate the hazard where possible
- Evaluate environmental and other workplace factors
- Consider specific job or jobsite hazards
- Implement a pre-determined rescue plan
- Know the three parts of a fall arrest system
- Select the proper equipment for each application
- Properly fit a harness
- Determine and reduce free fall distances
- Understand how to lower the maximum arresting force
- Select an appropriate anchor point
- Avoid incompatible connections to prevent snap hook roll-out and/or burst-out
- Inspect and maintain equipment
- Understand the limitations and requirements of the equipment
- Understand the consequences of not following or understanding manufacturer’s instructions
Additional training guidance can be found in ANSI/ASSP Z359.2-2023 Minimum Requirements for a Comprehensive Managed Fall Protection Program.
Role of Competent and Qualified Persons
The Competent Person (CP) and Qualified Person (QP) are key roles in a Fall Protection Program. Definitions vary from one jurisdiction to another, so refer to your employer or specific jurisdiction’s definitions for your FPP. The following definitions are taken from OSHA 1926.32 to explain the general intent and purpose of the aforementioned roles.
A Competent Person is, “…capable of identifying existing and predictable hazards in the surroundings or working conditions which are unsanitary, hazardous, or dangerous to employees, and who has authorization to take prompt corrective measures to eliminate them.”
Generally, a Competent Person is designated by the employer as someone who is familiar with the Fall Protection Program, equipment, and training. The key to the CP role is that they can predict hazards associated with fall protection and have a level of authority through the employer to take corrective actions when issues arise. A CP can be a trades person, safety professional, supervisor, area manager, or several other titles.
For example, a site safety supervisor has the role of ensuring employee safety. To be a Competent Person, this supervisor must have the ability to identify fall hazard issues (fall distance, equipment condition, arresting force, anchor strength, training, etc.) and have the authority to take corrective action (change anchor locations, stop work, remove equipment from service, retrain, etc.).
The person in this important role should be able to:
- Identify existing or predictable hazardous or dangerous conditions related to the workplace, work processes, and the safety at heights program.
- Establish controls on identified existing or predictable fall hazards according to the hierarchy of controls.
- Understand how to select, inspect, use, store, and maintain personal equipment for fall protection.
- Identify existing or predictable hazardous or dangerous conditions in a personal fall arrest system and any component thereof.
- Train workers at risk of falling from heights in accordance with standards and regulation.
- Apply a working knowledge of applicable standards and regulations.
A Qualified Person is one who, “…by possession of a recognized degree, certificate, or professional standing, or who by extensive knowledge, training, and experience, has successfully demonstrated his ability to solve or resolve problems relating to the subject matter, the work, or the project.”
The Qualified Person can best be understood as a “subject matter expert.” A QP is usually a supportive role to the Fall Protection Program and acts as a “problem solver” due to their specialized knowledge or ability relating to the subject matter.
For example, imagine a Competent Person has identified a potential issue regarding the strength of an anchorage in a building. In this situation, the subject matter is the strength of a building member. Therefore, the subject matter expert, or Qualified Person, would be a structural engineer who is familiar with fall protection and the building materials in question. If a Competent Person were to identify an issue with equipment deteriorating, the subject matter expert, or Qualified Person, could be the equipment manufacturer. The key to a Qualified Person is their specialized ability to solve issues related to the subject.
It is common for organizations to have several Competent and Qualified Persons according to the needs of the Fall Protection Program and varying scopes of work.
For further discussion of the roles of the Competent Person and Qualified Person, and other roles within a Fall Protection Program, see ANSI/ASSP Z359.2-2023.
Components of a Personal Fall Arrest System
The common components that make up a complete Fall Protection Program are usually referred to as the ABCs of fall protection:
- Anchorage
- Body support
- Connecting devices
Each one of these ABCs must be in place and properly used to provide maximum worker protection.
While each of these components is vital to worker safety, anchorage provides the foundational support, body support contains the worker, and the connecting device controls fall distances and forces. Careful consideration must be given to the selection, materials, construction, and inspection/maintenance of each of these components to ensure they work as intended and in concert with each other.
Anchorage/Anchorage Connector
OSHA defines an anchorage as a secure point of attachment for lifelines, lanyards, or deceleration devices. An anchorage is usually a fixed structural component that is part of an existing structure such as a beam, girder, column, or floor that can support the forces exerted in arresting a fall. The ANSI/ASSP Z359 standard introduces the term “anchorage connector” to refer to the component by which the connecting device is attached to the anchorage. The anchorage connector is the piece of equipment used to capture the anchorage. It may be a beam clamp, cross-arm strap, D-bolt, hook anchor, tripod, davit, or other piece of equipment. The anchorage connector serves to capture the anchorage structure for the attachment of lifelines, lanyards, or deceleration devices.
Regulations require anchorages for fall protection be independent from any anchorage used to support or suspend scaffolds and be capable of supporting 5,000 lb. per employee attached. Alternatively, anchorages can also be designed, installed, and used under the supervision of a Qualified Person as part of a complete personal fall arrest system which maintains a safety factor of at least two. Most all jurisdictions provide these options for anchorage strength: 5,000 lb. per employee or a 2:1 safety factor as supervised by a Qualified Person. Determining the strength of the anchorage is one of the QP’s most common tasks. The QP not only assesses the strength of the structure, but they also evaluate the location and elevation of the anchorage to ensure the workers will not come into contact with a lower level should a fall occur.
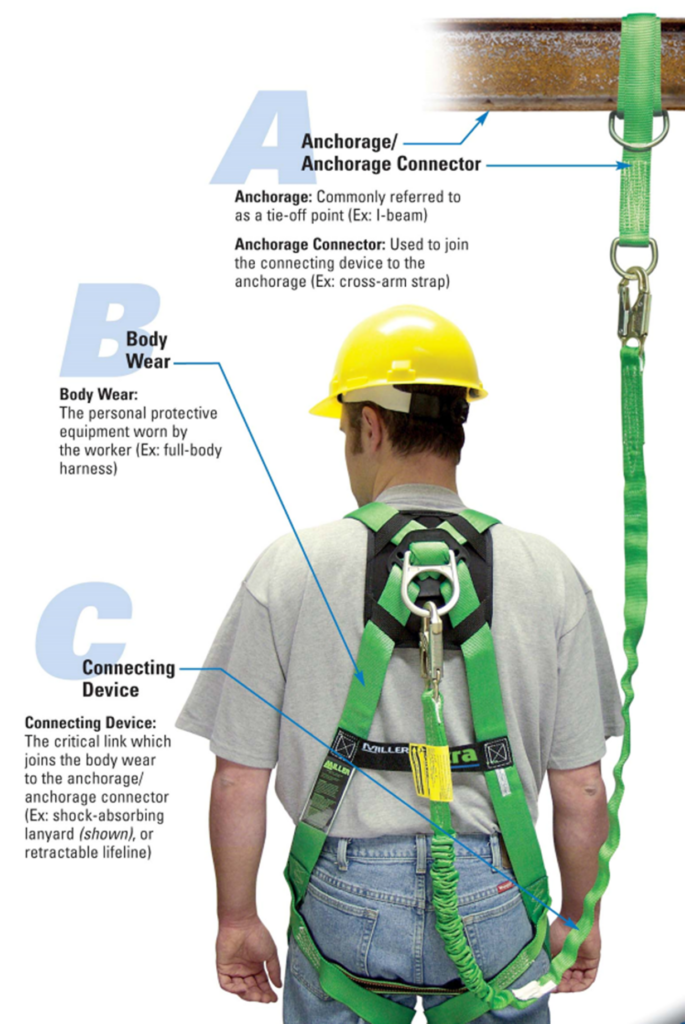
Body Support
A body support, or full body harness (FBH), is the component that is worn around the torso and pelvis. A FBH is the most common body support. A harness distributes forces to the strongest parts of the body, has multiple D-ring connection points for specific work needs, and keeps a worker upright at the end of a fall.
Full Body Harness
A full body harness is a body support device that distributes fall arrest forces across the shoulders, thighs, and pelvis. Full body harnesses have an upper back (dorsal) fall arrest attachment (usually a D-ring) for connection to the connecting device. There are thousands of harness designs available that have varying attachment points for use in worker positioning, fall prevention, suspension, or ladder climbing. Harnesses are available in a number of sizes with features according to the needs of the work like work-belts, comfort padding, adjustment options, tool/phone holders, and dozens of other features.
Common rules for harnesses include:
- The only form of body wear acceptable for fall arrest is the full-body harness.
- Full body harnesses should be selected based on the work environment (heat, visibility, belts, d-rings, etc.) and work to be performed.
- The upper chest (sternal) attachment may be used for fall arrest in special conditions if fall distances and forces are controlled.
- Harnesses must be inspected before each use and removed from service after a fall.
- Harnesses must be sized to fit, and users must be trained on how to adjust, wear, and make connections to the harness.
The use of body belts for fall arrest is illegal and dangerous. Fall arrest forces are directed to the center of the torso and are only supported by the soft tissue, spine, and ribs in the center of the body. A person in a body belt may double over, or slide out, and cannot remain suspended for very long. For these reasons, all jurisdictions disallow the use of body belts for fall arrest. Keep in mind that full body harnesses that incorporate a body belt are acceptable for use, and body belts alone can be used for travel restraint and some positioning applications.
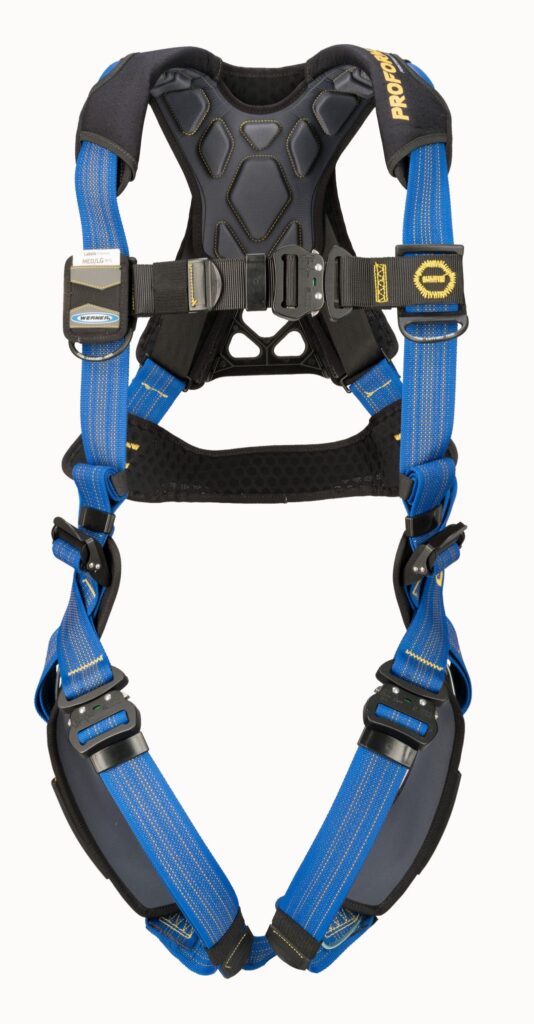
Connecting Devices
The connecting device is the link which joins the harness to the anchorage. It can be an energy-absorbing lanyard, positioning lanyard, self-retracting device, rope adjuster, fall arrester, or retrieval system. The connecting equipment will vary depending on the needs of the work, range of movement needed, anchorage location, and necessary capacity.
Connecting Devices for Personal Fall Arrest
In the event of a fall, energy absorption is very important. The forces generated in a fall are what injures the worker and loads the equipment and anchorage. All fall arrest systems must control energy, so the most common control method is using a connecting device that has an energy absorber. Connecting equipment usually comes equipped with an energy-absorbing element to reduce the forces transmitted to the user’s body in the event of a fall.
Self-retracting devices have an energy absorbing ability inside the unit, or externally in the line, to reduce free fall distance and energy loads from a fall. Fall arrest lanyards have an energy absorbing ability built into the design by having an external or internal energy absorber. Vertical lifelines, fall arresters, and rope adjusters used for fall arrest also have energy absorbers in the design, either at the anchor location or on the lanyard connecting to the lifeline.
Using energy absorbers properly will control forces on the worker, anchorage, and equipment to reduce the potential for injury. All regulations require that a worker cannot be exposed to more than 1800 lbs. of arresting force, and it is the proper use of an energy absorber that accomplishes this goal. See Section 5 of this User Guide for guidance on calculating fall clearance and accounting for energy absorber deployment.
Connecting Devices for Personal Fall Arrest
The connecting device for positioning and travel restraint is often a simple lanyard that is constructed of rope, web, or wire rope. Typically, this lanyard is without an energy absorber. Since travel restraint systems do not involve any free fall distance and positioning systems are limited to free falls with less than 2 feet of free fall, an energy absorber is not necessarily needed to control forces.
Connecting devices may also include specialized positioning assemblies for rebar work. These are constructed of chain or web. All positioning devices are intended to reduce the potential for free fall to a distance of 2 feet or less. Restraint lanyards are offered in differing lengths due to a jobsite’s specific needs. These lanyards prevent the user from reaching a fall hazard zone entirely.
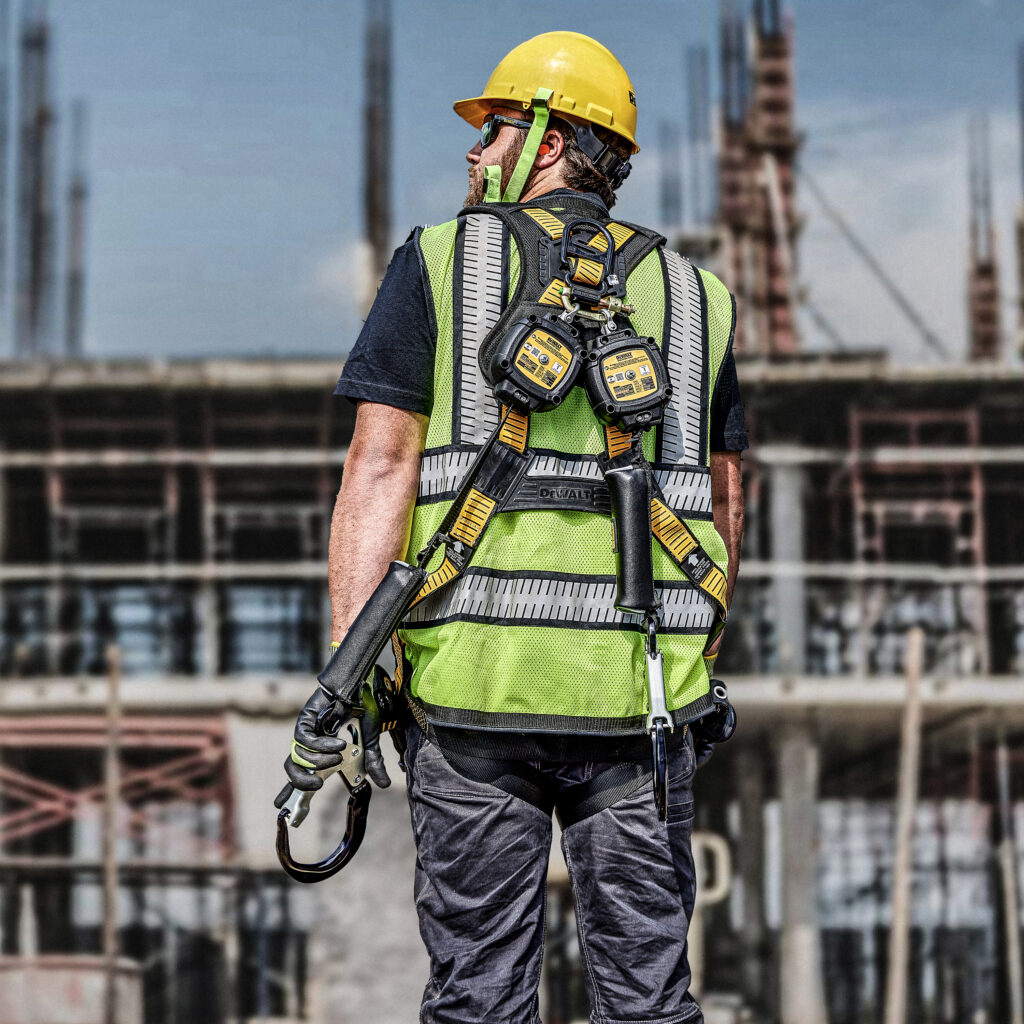
Selection of Personal Fall Protection Equipment
This section aims to provide general instruction for the selection of fall protection equipment. There are thousands of options available and several exceptions to this list below. However, every system must have an anchorage, body support, and connecting device.
Fall Arrest
As a general principle, fall arrest systems are used when other, more effective forms of fall protection cannot be used. If a fall hazard cannot be eliminated, guarded, or restrained against, fall arrest systems are the next option. The following is recommended:
- Anchorage – Support structure capable of supporting 5,000 lb. per employee attached, or designed, installed, and used under the supervision of a Qualified Person as part of a complete personal fall arrest system which maintains a safety factor of at least two.
- Anchorage Connector – Anchor sling, I-beam trolley, or other anchorage connector.
- Body Support – Full body harness (sized and fitted correctly) with the correct D-ring locations for the work performed.
- Connecting Device – Energy-absorbing lanyard or self-retracting device, or lifeline with a fall arrester/rope adjuster.
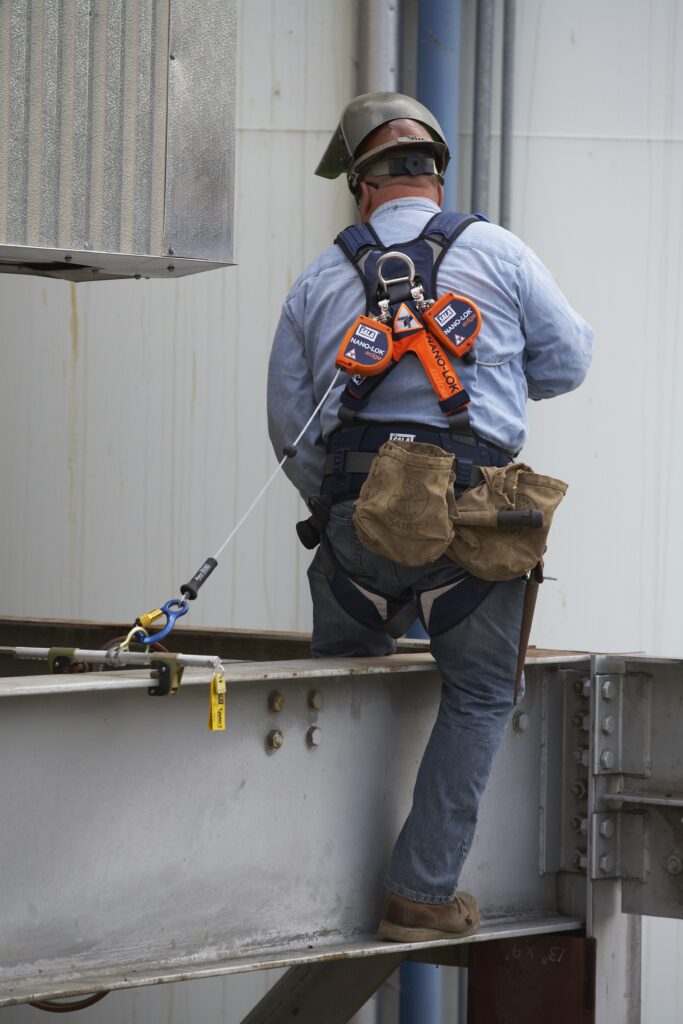
Work Positioning
A work positioning system is used to hold a worker in place while allowing a hands-free work environment at elevated heights. The free fall must be limited to 2 feet or less. A fall arrest system* should be used in conjunction with a work positioning system when the user is at an elevated height. The following is recommended:
- Anchorage- Support structure such as a ladder or vertical rods, large anchorage snap hook, or carabiner.
- Body Support – Full body harness with hip D-rings for the attachment of work positioning equipment.
- Connecting Device – Rebar assembly or positioning lanyard connecting the harness (usually hip connections) to the anchorage.
*A separate fall arrest system, usually an energy-absorbing lanyard or self-retracting device connected to the back harness D-ring, is recommended.
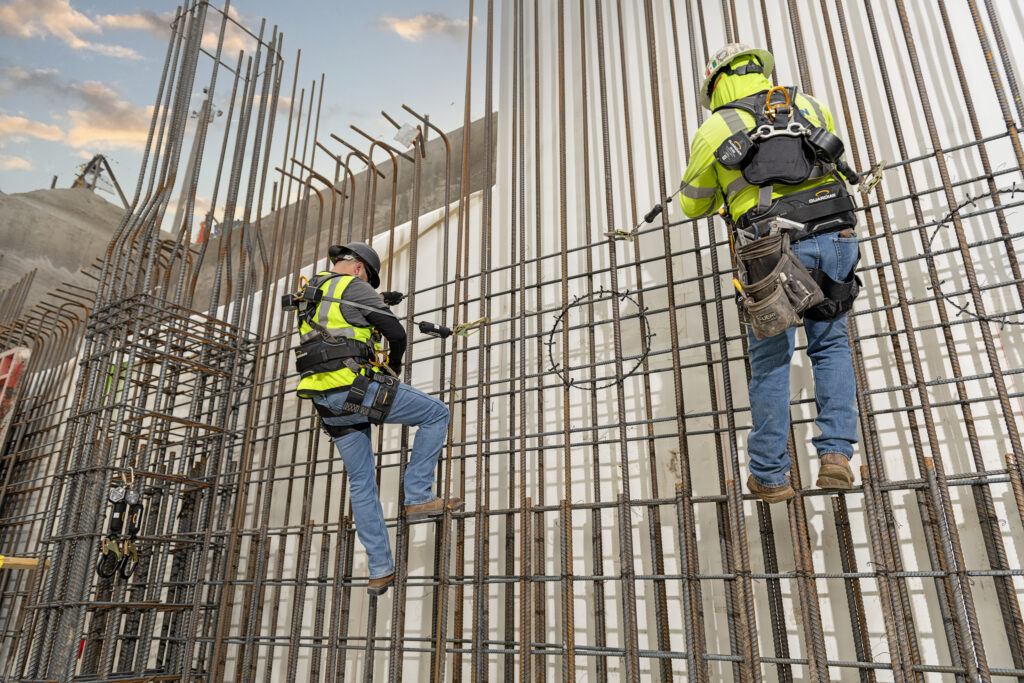
Travel Restraint
A travel restraint system prevents the range of movement a worker has and prevents them from reaching a location where a free fall hazard exists. The following is recommended:
- Anchorage- Support structure, anchor sling, beam clamp, or roof anchor system.
- Body Support – Full body harness or body belt with back mounted D-ring.
- Connecting Device – Positioning lanyard, lifeline, and rope adjuster with lanyard.
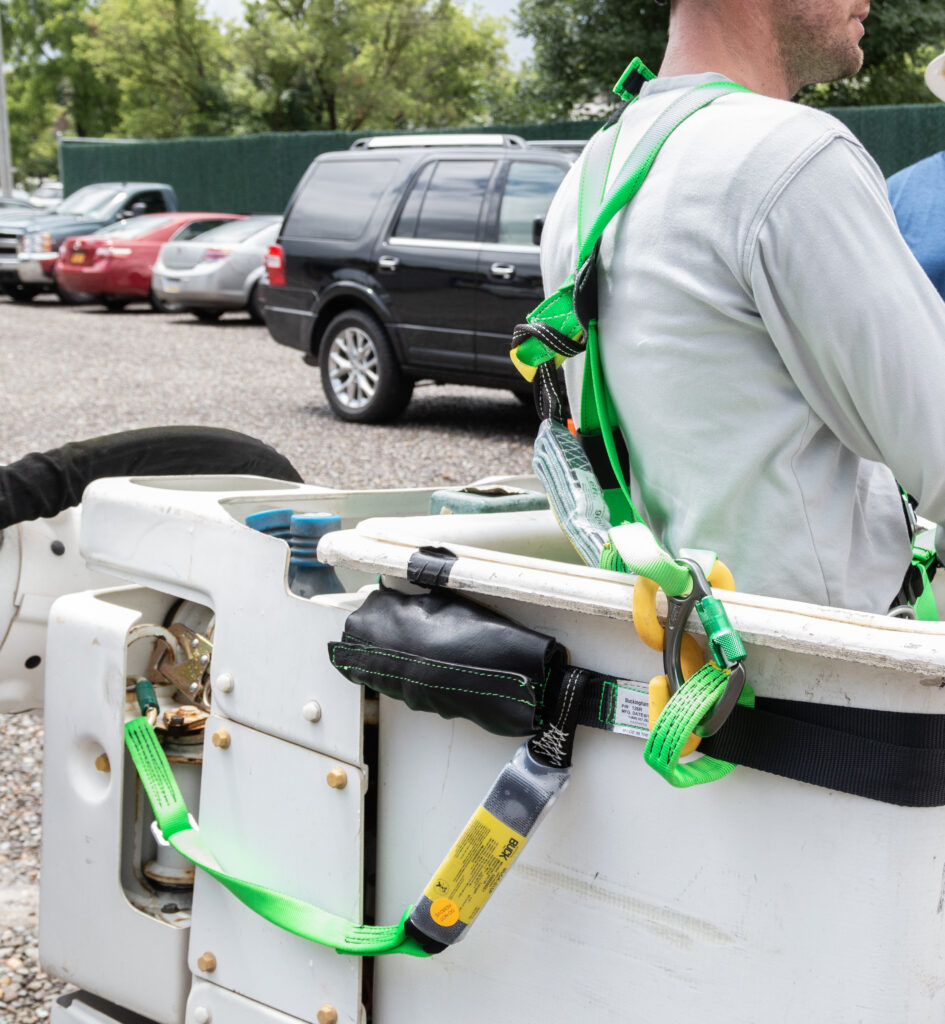
Suspension/Personnel Riding Systems
Suspension systems are used widely in industries where workers need to be suspended for work tasks. These systems are designed to support a worker vertically while allowing a hands-free work environment. A window cleaners’ rope, descent device, suspension chair, harness, and independent fall arrest system are examples of a suspension system. The following is recommended:
- Anchorage- Support structure (two separate anchorages are needed– one for the suspension system and one for the fall arrest system), anchor sling, tripod or davit, or engineered anchors in building.
- Body Support – Full body harness with suspension seat (may be integral), fall arrest D-ring, descent control D-ring.
- Suspension Connecting Device – Suspension system to ascend and descend (rope descent device).
- Fall Arrest Connecting Device – Lifeline and fall arrester with energy absorption and independent anchorage.
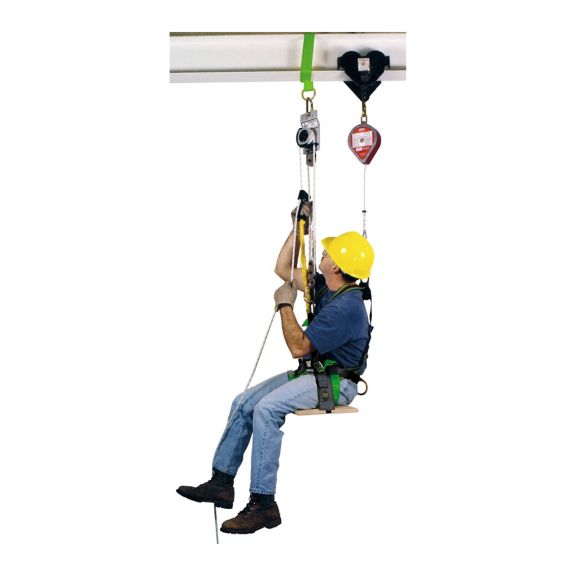
Retrieval/Rescue
The retrieval system is primarily used in confined space applications where workers must enter tanks, manholes, etc. and may require retrieval from above should an emergency occur. The following is recommended:
- Anchorage- Support structure (ground, well, foundation, etc.), tripod, or davit.
- Body Support – Full body harness with back (and possibly shoulder) D-rings.
- Connecting Device – Self-retracting device with retrieval capabilities and a personnel-rated hoist when ladder access is not available.

Ladder Climbing/Permanent Fixed Ladders
Fall protection is not legally required when using a portable ladder as long as the portable ladder is being used correctly. However, fall protection is required on fixed ladders that extend more than 24 feet (7.3 m) above a lower level. By 2036, all fixed ladders whether existing, new, or replaced, must be equipped with a personal fall arrest system or ladder safety system.
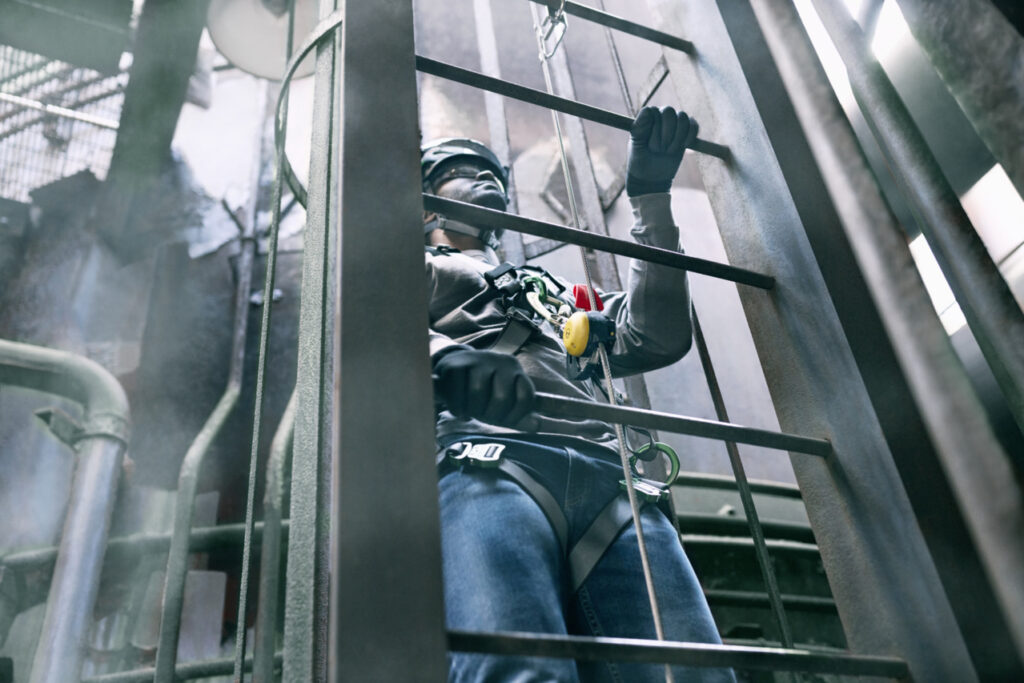
Flexible Line Fall Arrest Systems
- Anchorage – Permanent ladder meeting the requirements of OSHA 29 CFR 1910.23 and manufacturer strength requirements.
- Anchorage Connector – Fixed wire rope lifeline with intermediate supports and a mobile fall arrester.
- Body Support – Full body harness equipped with front (sternal) D-ring for attachment to ladder climbing fall arrest system.
- Connecting Device – mobile fall arrester (device that travels up the cable/line) compatible with the wire rope with a connecting
snap hook, or carabiner, and energy absorption design.
Rigid Rail Fall Arrest Systems
- Anchorage -Permanent ladder meeting the requirements of OSHA 29 CFR 1910.23 and manufacturer strength requirements.
- Anchorage Connector – Rigid rail or track.
- Body Support – Full body harness equipped with front (sternal) D-ring for attachment to ladder climbing fall arrest system.
- Connecting Device – mobile fall arrester (device that travels up the cable/line) compatible with the rail with a connecting snap
hook, or carabiner, and energy absorption design.
Evacuation/Controlled Descent Systems*
- Anchorage- Support structure, anchor sling, beam clamps, beam trolleys, fixed D-rings, etc.
- Body Support – Full body harness with waist (ventral) or sternal (chest) D-ring.
- Connecting Device – Descent control device with compatible rope and connecting snap hooks or carabiners.
* For rescue and evacuation applications, a single rope or evacuation system can be used without an independent fall arrest system. It is recommended a rescue plan incorporates a fall arrest system, in addition to the rescue system, to increase the level of security. However, in an emergency, a second fall arrest system is sometimes infeasible. If the controlled descent system is being used in a non-emergency application, a separate independent fall arrest system is required.
See SUSPENSION/PERSONNEL RIDING SYSTEMS.
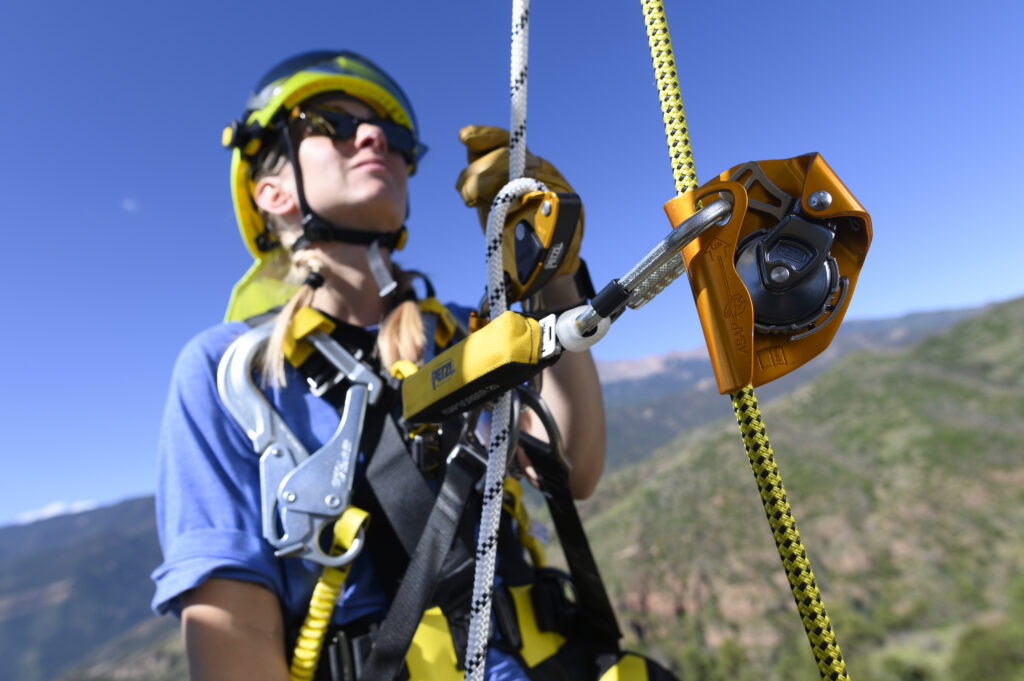
Selection of Personal Fall Equipment
Download the Personal Fall Protection Equipment chart below.
Planning the Use of Systems
First Steps
Begin by assessing the work site for fall hazards (height, frequency of work, anchorages available, paths of travel, etc.). All hazards identified in this evaluation must be addressed with suitable controls planned and implemented. This information is imperative for selecting the right equipment for the work being performed i.e. harness D-rings, range of movement, forces generated in a fall, and fall clearance needs.
Then, plan the system(s) prior to starting the actual work. Consider all possible paths the user’s movement may take and all factors that could affect the user’s safety before, during, and after a fall anywhere along these paths.
Select the anchorage and anchorage connectors, type of system, and harness to match the work, workplace hazards, and environment. Consider the following points when planning the system(s):
- Regulations – Understand all federal, state or provincial, and local regulations pertaining to fall protection before selecting and using the equipment.
- Rescue Planning – A thorough rescue program should be established prior to using fall protection equipment. It is vitally important to minimize the time between a fall occurrence and the worker’s medical attention.
- Training – All workers should be trained by a Competent Person in the proper use of fall protection products.
- Inspection – All fall protection equipment must be inspected prior to each use.
- Warnings – Always read and follow all instructions and warnings contained on the product and packaging before using any fall protection equipment.
- System Components – Fall arrest systems can be made from available components, so it is important that components are compatible with each other when assembled. Only components compatible with one another should be used. Do not alter, remove, or modify any piece of the equipment.
- Product/System Preferences – If there are any doubts about which fall protection products to use, contact the manufacturer for assistance.
- Sharp Edges – If work must be performed near unavoidable sharp edges, plan to cover the sharp edge and protect the fall protection equipment by use of padding or other means.
- Equipment Removal – After a fall occurs, all components of the fall arrest system should be identified, segregated, and removed from service.
Anchorage and Anchorage Systems
Determine anchorage locations to ensure that the user will be continuously connected when exposed to fall hazards. Select anchorages that are stable and have the required strength. Select anchorage locations above the work area and higher than the harness attachment point whenever feasible. Using an anchorage location lower than the harness attachment point will increase forces on the user’s body, free fall, and total fall distances. Choose a location that will prevent swing falls and impact with objects in, or adjacent to, the fall path. Swing falls increase the fall distance. Plan the types of anchorage connectors needed.
Carefully select the locations of the anchorages to:
- Reduce possible free fall distance.
- Prevent swing fall hazards.
- Provide clear space in the potential fall paths to avoid striking an object.
Free Fall Distance, total Fall Distance, and Deceleration Distance
Personal fall arrest systems must be selected and rigged to ensure that potential free fall distances will never exceed 6 ft. (1.8 m) as required by regulations. Always refer to the manufacturer’s instructions to determine the deceleration distance and elongation that must be taken into consideration.
Most safety regulations provide exceptions for applications where free fall distances must exceed 6 ft. For example, a lack of an acceptable anchorage. A foot-level anchorage is approximately 5 ft. below the user’s D-ring assuming the average worker is 6 ft. tall. This additional 5 ft. may increase free fall. In these situations, free fall distances can exceed 6 ft. if fall arrest forces and clearances are still acceptable.
Several fall protection products exist for these scenarios. Higher capacity energy absorbers/lanyards and self-retracting lifelines designed for foot-level anchorages are the most common. These products are designed to have the capacity to handle increased free fall distances. However, users must be aware that when deceleration distances increase, more clearance is required, and contact with edges will likely occur. Always refer to the manufacturer’s instructions.
Total fall distance is the sum of free fall distance and deceleration distance. The worker’s height and the elongation of the system (stretch and deceleration distances of connecting components and equipment) must be added to total fall distance to allow for clearance. It is best practice to add an additional safety factor of 2 ft. below the worker’s feet.
Free fall distance must be estimated to assemble the worker’s equipment safely and select the appropriate type of connecting device. For example, for a 6 ft. worker using a 6 ft. lanyard, the total fall clearance required from the anchorage to the below surface would be 18 ft. (5.5 m). This is calculated by adding the original length of the lanyard (6 ft.), the deceleration distance (a 4 ft. maximum elongation of the energy absorber), harness stretch (1 ft.), distance from the worker’s feet to the D-ring (5 ft.), and safety factor (2 ft.).
In this case, if the clearance available is less than 18 ft., an alternative solution is needed to reduce the fall clearance required. A shorter lanyard length, higher anchorage location, or different connecting device such as a self-retracting lanyard may be the solution. If the fall clearance is 18 ft. or more, there is sufficient total fall distance available, and the 6 ft. lanyard is acceptable to use. Clearance requirements will change with every application since the equipment, anchorage, and worker location changes. Therefore, it is important that users, Competent Persons, and the Qualified Persons evaluate each location. Consult manufacturer’s instructions for specific details about each products’ clearance requirements.
Note: Do not ever tie a knot in a lanyard to shorten it as this reduces its strength by more than 50%. Instead, purchase an adjustable lanyard and adjust it to the proper working length.
User Movements
Identify all necessary movements of the user and the materials and equipment needed to perform the planned work. The plan should ensure there is no crossing or tangling of equipment amongst workers. Users must not clamp, knot, modify, or otherwise prevent the equipment from functioning properly. Provide training on proper use of fall protection and establish controls to prevent these occurrences. Additional revisions to clearance requirements must be performed when users are working in non-standing positions. These work conditions will increase total fall distance.
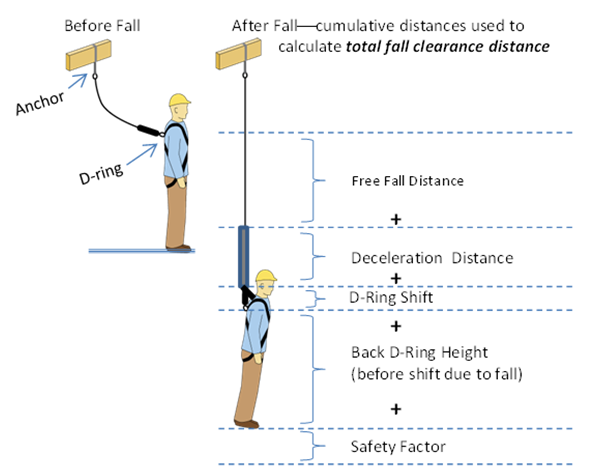
Pendulum (Swing) Falls
Swing falls can occur when the system is not anchored directly above the user. The force of striking an object in a pendular motion can cause serious injury. Always minimize swing falls by working as directly below the anchorage point as possible.
Clear Space in Fall Path
Plan for enough clearance in all potential fall paths to prevent striking an object. The amount of clearance needed depends upon the type of equipment used and the location of the anchorage. Consult the manufacturer’s instructions for the clearance requirements of the chosen equipment.
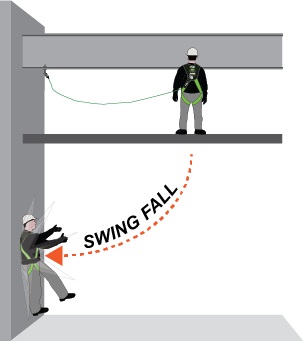
Rescue and Evacuation
The user must have a rescue plan and the means at hand to implement it. The plan must take into account the equipment and special training necessary for a prompt rescue under all foreseeable conditions. If the rescue is from a confined space, additional entry and rescue provisions apply (i.e. OSHA regulations 29 CFR 1910.146 and 1926.1211). Although a rescue plan and the means to implement it must always be in place, it is a good idea to provide means for user evacuation without assistance of others. This will usually reduce the time it takes for the fallen worker to get to a safe place and reduce, or prevent, risk to rescuers. Focus on prevention, control methods, trauma straps, suspension trauma relief to extend rescue times, hierarchy of controls, etc.
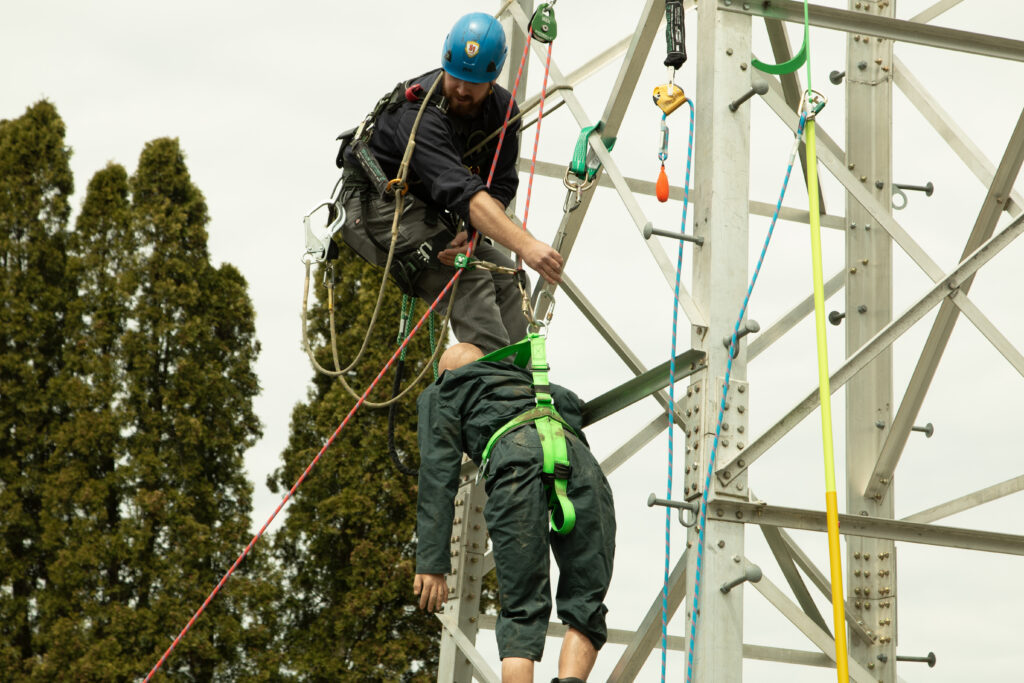
Inspection of Fall Protection Equipment
Fall protection equipment must be visually inspected before each use. A Competent Person must also inspect the equipment for wear on a regular basis (either monthly, every 6 months, or annually depending on the frequency of use, environment in which the equipment is used, and local safety regulations). Frequent use and use in severe environments will require more frequent inspections.
Inspection details are available in the instructions provided with the fall protection equipment. Each inspection should be documented. It is important to follow any specific instructions that are provided with the equipment at the time of purchase. Instructions should be stored in a location where they are readily available to the users. Most instructions are also available in digital form on manufacturer websites.
Inspect all equipment according to the manufacturer’s instructions. If required by the manufacturer, return the equipment to the manufacturer for inspection, repair, or recertification.
Remove equipment from service if a stress indicator or warning system has been activated. Follow manufacturer’s instructions for disposal of the equipment.
If a fall has been arrested by the fall protection equipment, immediately remove all components of the system from service and follow the manufacturer’s instructions for disposal.
Harness and body Belt Inspection
Always refer to the specific instructions provided with the harness for inspection details.
Common inspection points include:
- Webbing – Grasp the webbing with both hands 6 in. (152 mm) to 8 in. (203 mm) apart. Bend the webbing in an inverted “U.” The surface tension that results will make any damaged fibers or cuts easier to detect. Follow this procedure the entire length of the webbing, inspecting both sides of each strap. Look for frayed edges, broken fibers, pulled stitches, cuts, burns, and chemical damage.
- D-Rings/Back Pads – Check D-rings for distortion, cracks, breaks, corrosion, and rough or sharp edges. D-rings should pivot freely. D-ring back pads should also be inspected for damage.
- Attachment of Buckles – Inspect for any unusual wear, frayed or cut fibers, or broken stitching of the buckle or D-ring attachments.
- Tongue/Grommets – The tongue receives heavy wear from repeated buckling and unbuckling. Inspect for loose, distorted, or broken grommets. Webbing should not have additional punched holes.
- Tongue Buckles – Tongue buckles should be free of distortion in shape and motion. They should overlap the buckle frame and move freely back and forth in their socket. The roller should turn freely on frame. Check for distortion or sharp edges.
- Friction and Mating Buckles – Inspect the buckle for distortion. The outer bars and center bars must be straight. Pay special attention to corners and attachment points at the center bar.
- Quick-Connect Buckles – Inspect the buckle for distortion. The outer bars and center bars must be straight. Make sure the dual-tab release mechanism is free of debris and engages properly.
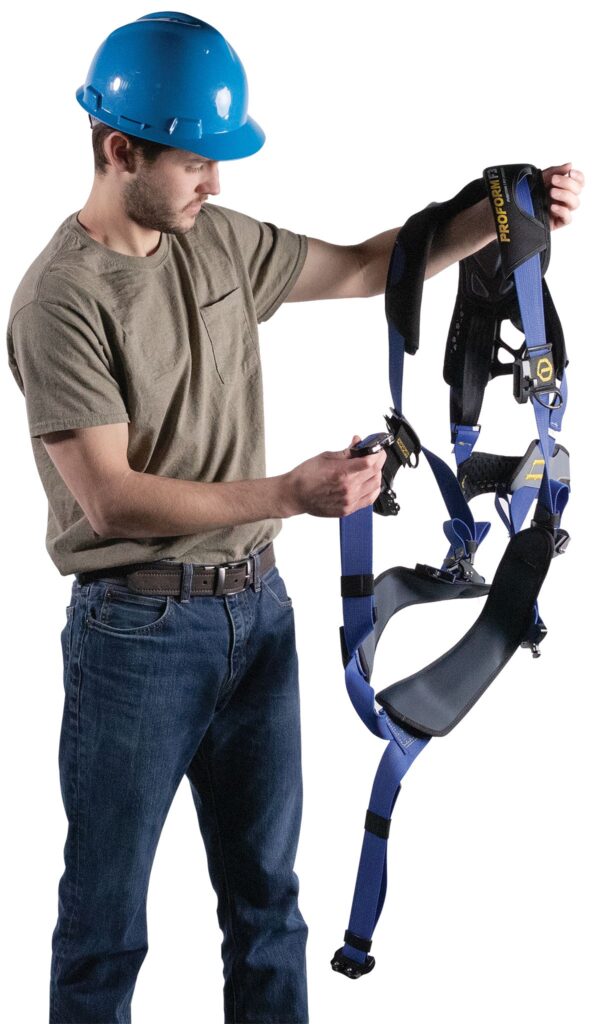
Lanyard Inspection
When inspecting lanyards, begin at one end and work to the opposite end, slowly rotating the lanyard so that the entire circumference is checked. Always refer to the specific instructions provided with the lanyard for inspection details.
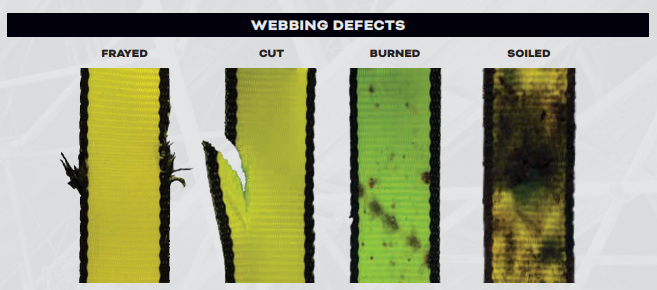
Common inspection points include:
Hardware
- Snaps – Inspect closely for hook and eye distortions, cracks, corrosion, or pitted surfaces. The keeper (latch) should fit into the nose without binding and should not be distorted or obstructed. The keeper spring should exert sufficient force to firmly close the keeper. Keeper locks must prevent the keeper from opening when the keeper closes.
- Thimbles – The thimble must be firmly seated in the eye of the splice, and the splice should have no loose or cut strands. The edges of the thimble must be free of sharp edges, distortion, or cracks.
Lanyards
- Wire Rope Lanyard – While rotating the wire rope lanyard, watch for cuts, frayed areas, or unusual wear patterns on the wire. Broken strands will separate from the body of the lanyard.
- Web Lanyard – While bending webbing over a pipe or mandrel, observe each side of the webbed lanyard. This will reveal any cuts or breaks. Swelling, discoloration, cracks, and charring are obvious signs of chemical or heat damage. Observe closely for any breaks in stitching.
- Energy-Absorbing lanyard – While bending webbing over a pipe or mandrel, observe each side of the lanyard. This will reveal any cuts or breaks. Swelling, discoloration, cracks, and charring are obvious signs of chemical or heat damage. Observe closely for any breaks in stitching. Look for the warning flag or signs of deployment. If the flag has been activated, remove the lanyard from service.
- Rope Lanyard – Rotate the rope lanyard while inspecting from end-to-end for any fuzzy, worn, broken, or cut fibers. Weakened areas from extreme loads will appear as a noticeable change in original diameter. The rope diameter should be uniform throughout, following a short break-in period.
- Energy- Absorber Pack – The outer portion of the pack should be examined for burn holes and tears. Stitching on areas where the pack is sewn to D-rings, belts, or lanyards should be examined for loose strands, rips, and deterioration. An energyabsorbing lanyard or self-retracting lifeline is composed of only one strength member (i.e., webbing, rope, steel, cable). Substandard design, poor quality workmanship, excessive exposure to UV light or chemicals, physical damage, improper storage, or inadequate inspection can lead to lanyard/lifeline failure.
Self-Retracting Lifeline Inspection
Always refer to the specific instructions provided with the self-retracting lifeline for inspection details.
Common inspection points include:
- Check Housing – Before every use, inspect the unit’s housing for loose fasteners and bent, cracked, distorted, worn, malfunctioning, or damaged parts.
- Retraction and Tension – Test the lifeline’s retraction and tension by pulling out the lifeline and allowing it to retract back into the unit. Always maintain a light tension on the lifeline as it retracts. The lifeline should pull out freely and retract all the way back into the unit. Do not use the unit if the lifeline does not retract.
- Lifeline – The lifeline must be checked regularly for signs of damage. Inspect for cuts, burns, corrosion, kinks, frays, or worn areas. If the lifeline is made of webbing, inspect sewing for loose, broken, or damaged stitching.
- Braking Mechanism – The braking mechanism must be tested by grasping the lifeline above the impact indicator and applying a sharp steady pull downward to engage the brakes. There should be no slippage of the lifeline while the brakes are engaged. Once tension is released, the brakes will disengage and the unit will return to its retractable mode. Do not use the unit if the brakes do not engage.
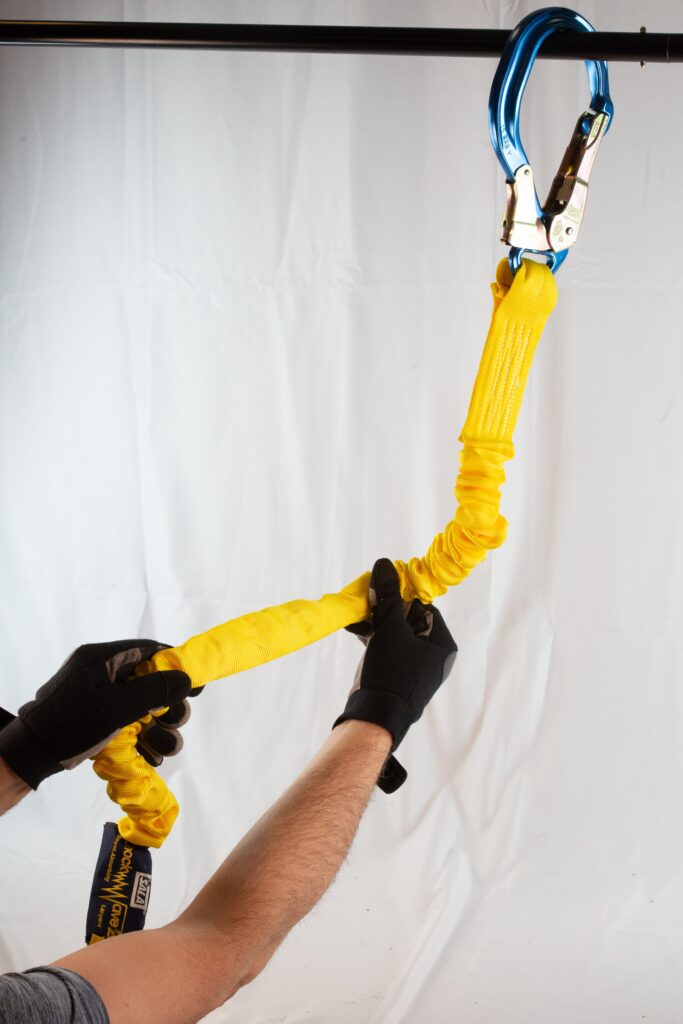
Hardware
- Snap Hooks – If equipped with a load indicator, it will be located at, on, or near, the snap hook. The swivel eye will elongate and expose a red area when subjected to fall arresting forces. Do not use the unit if the load impact indicator has been activated. Inspect closely for hook and eye distortions, cracks, corrosion, or pitted surfaces. The keeper (latch) should sit into the nose without binding and should not be distorted or obstructed. The keeper spring should exert sufficient force to firmly close the keeper. Keeper locks must prevent the keeper from opening when the keeper closes.
- Thimbles – The thimble must be firmly seated in the eye of the splice, and the splice should have no loose or cut strands. The edges of the thimble must be free of sharp edges, distortion, or cracks.
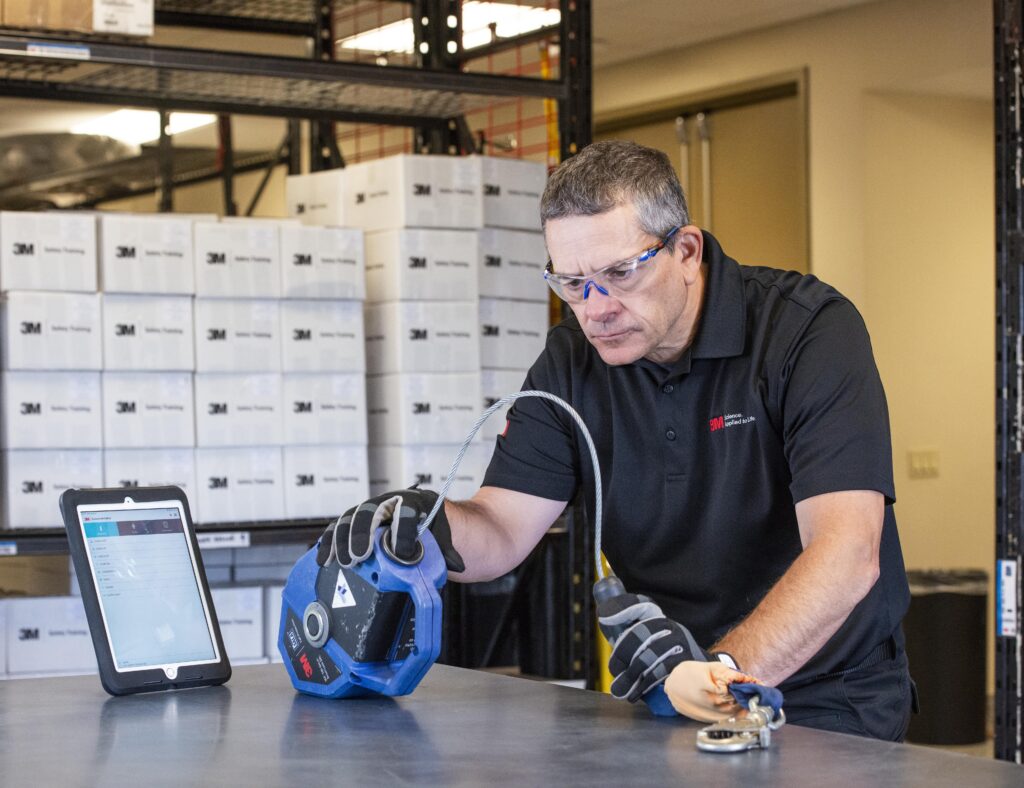
Examples of Improper Connections
The integrity of a fall protection system depends on proper connection of all its components. The following warnings should be heeded to avoid improper connections:
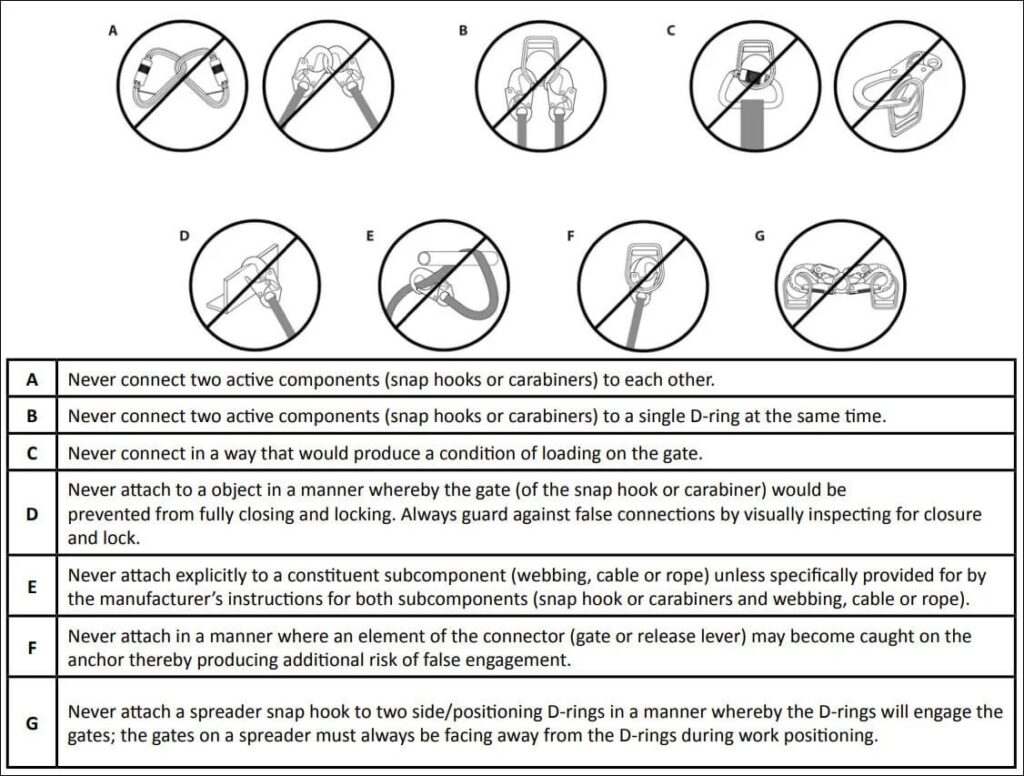
Cleaning, Maintenance, and Storage
Basic care of fall protection equipment will extend the life of the unit and will contribute toward its performance. Proper storage and maintenance after use are as important as cleansing the equipment of dirt or contaminants. Always refer to the instructions provided with the equipment for specific cleaning, maintenance, and storage requirements.
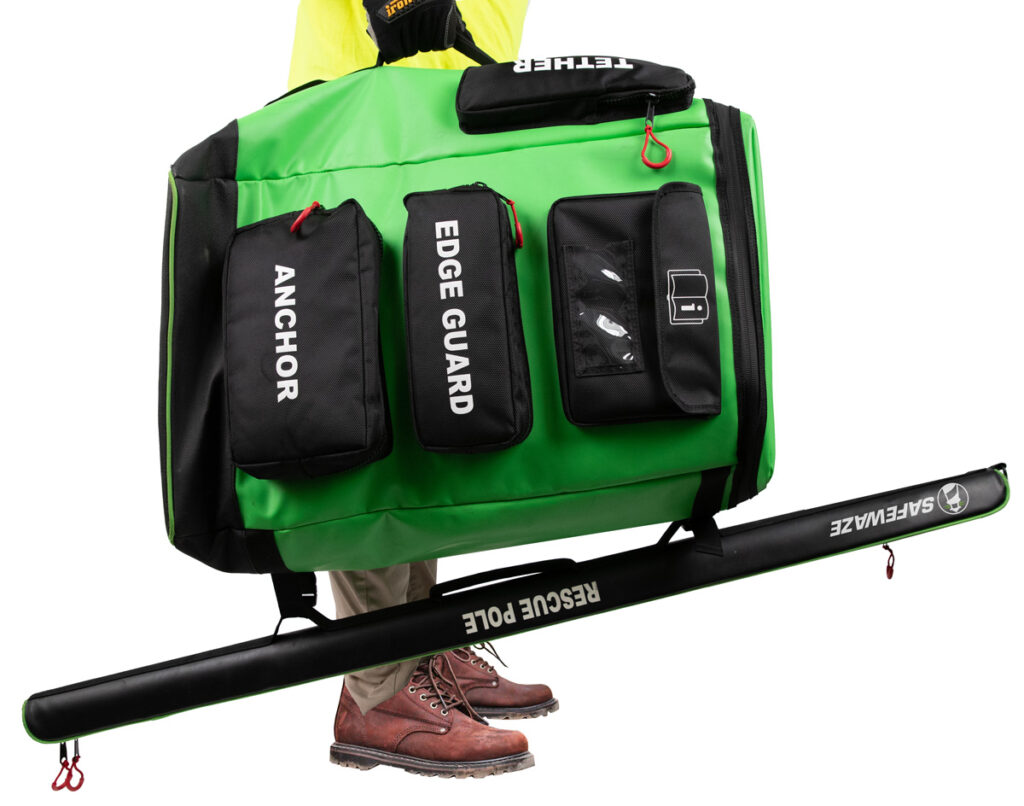
Common requirements include:
- Nylon or Polyester – Remove all surface dirt with a sponge dampened in plain water. Squeeze the sponge dry. Dip the sponge in a mild solution of water and commercial soap or detergent. Work up a thick lather with a vigorous back and forth motion. Wipe with a clean cloth. Hang freely to dry, but away from excessive heat.
- Housing – Periodically clean the unit using a damp cloth and mild detergent. Towel dry.
- Drying – Equipment should dry thoroughly without close exposure to heat, steam, or long periods of sunlight.
When not in use, fall protection equipment should be stored in a cool, dry, and clean place out of direct sunlight. Avoid areas where heat, moisture, light, oil, chemicals (or their vapors), or other degrading elements may be present.
Equipment that is damaged or in need of maintenance should NOT be stored in the same area as usable equipment. This prevents damaged equipment being mistakenly used.
Heavily soiled, wet, or otherwise contaminated equipment should be properly cleaned and dried prior to storage.
A formal inspection by a Competent Person should be performed prior to using equipment that has been stored for a long period of time.
Definitions
The following definitions were extracted from OSHA or ANSI at the time this document was published. Where the aforementioned did not define a term, the ISEA Fall Protection Product Group members supplied one. Definitions change and are updated. Refer to the most current version of standards and documents for more information.
A secure point of attachment for lifelines, lanyards, or deceleration devices.
A component or subsystem that functions as an interface between the anchorage and a fall protection, work positioning, rope access, or rescue system for the purpose of coupling the system to the anchorage.
A strap that is secured around the waist and is used for positioning or restraint only. Body belts are not used for fall arrest.
A design of straps which is secured about a person in a manner to distribute fall arresting forces over at least the thighs, pelvis, waist, chest, and shoulders with provisions for attaching it to other components of a personal fall arrest system.
A device for holding the body belt or body harness closed around the employee’s body by attaching straps or webbing segments together or to themselves.
- Tongue Buckle/Grommet Buckle: An integral connector similar to a standard belt buckle whereby a webbing strap is inserted through the buckle and the buckle tongue through the appropriate grommet hole.
- Friction Buckle: An integral connector whereby the webbing passes over the knurled bar and back down between the knurled bar and frame to adjust and tighten webbing straps.
- Mating Buckle: An integral connector whereby a center bar is pushed through a square link. Webbing is then tightened for proper fit.
- Quick-Connect Buckle: An integral connector for leg and chest harness straps that interlock for easy use with a dual-tab release mechanism to prevent accidental opening.
A connector component generally composed of a trapezoidal or oval shaped body with a normally closed gate or similar arrangement which may be opened to permit the body to receive an object and, when released, automatically closes to retain the object. Carabiners used in personal fall protection should be self-closing and self-locking and only capable of opening with two consecutive actions by the user.
An enclosed area that is large enough that an employee can bodily enter and has the following characteristics: its primary function is something other than human occupancy, has restricted entry and exit, and may contain potential or known hazards.
A mechanism or device used to join together components of a personal fall arrest system (a carabiner) or parts of a component within the system (a D-ring on a body harness).
A bucket, tool bag, or similar device used to hold or transport tools or other equipment.
A fall protection system that is designed so that there is no unprotected exposure to an elevated fall hazard.
A device that provides a means of lowering an individual from height at a controlled rate of descent.
A device that absorbs or dissipates energy during a fall arrest.
The additional vertical distance a falling person travels (excluding lifeline elongation and free fall distance) before stopping, from the point at which the deceleration device begins to operate. It is measured as the distance between the location of a person’s body harness attachment point at the moment of activation (onset of fall arrest forces) of the deceleration device during a fall, and the location of that attachment point after the person comes to a full stop.
An integral “D” shaped connector commonly found on body wear and some anchorage connectors which allows for attaching a connecting device (lanyard, lifeline, or deceleration device). ANSI may refer to them as attachment elements (O-ring, soft loops, etc.).
A component of a personal fall arrest system that allows dissipation of energy by extending deceleration distance to reduce fall arrest forces.
A specially designed lanyard that elongates during a fall to significantly reduce fall arrest forces. These are also referred to as shock/stretch absorbing lanyards.
A safety device or warning flag which serves to let a user know that a component of a personal fall arrest system has been involved in a fall, or has been exposed to equivalent forces, and should be removed from service. These are also referred to as visual and/or impact indicators.
A self-retracting lifeline/lanyard with a quick-activating braking system that limits a free fall.
A stationary anchor point that is capable of supporting at least twice the maximum potential force of the fall arrest system.
The act of falling before the personal fall arrest system begins to apply force to arrest the fall.
The vertical displacement that a person falls before the fall arrest system begins to arrest the fall.
Buckles, D-rings, snap hooks and associated connectors which are used to attach components of a personal fall arrest system or parts of a component within the system together.
A support system limiting an employee’s drop or fall from the ladder, and which may incorporate friction brakes, lifelines and lanyards, or sliding attachments.
A flexible line of rope, wire rope/cable, or webbing which generally has a connector at each end for securing a body belt or body harness to a lifeline, deceleration device, or anchorage.
A component consisting of a flexible line for connection to an anchorage at one end to hang vertically (vertical lifeline), or for connection to anchorages at both ends to stretch horizontally (horizontal lifeline), and which serves as a means for connecting other components of a personal fall arrest system to the anchorage.
A snap hook that includes a locking mechanism to keep the hook closed and locked until manually unlocked and opened.
An area or surface to which a person can fall.
The peak force on the body during arrest of a fall by the fall arrest system.
An arrangement of components that together will arrest a person in a fall from a working level. It typically consists of an anchorage, connecting device and body harness, and may include a lanyard, deceleration device, lifeline or a combination of these.
A container designed to transport materials by means of a lifting element.
A device with a self-managing tether where the tether is automatically drawn back into the housing.
Unintentional disengagement of a snap hook caused by the gate being depressed under torque or contact while twisting or turning. This event is a particular concern with single-action snap hooks that do not have a locking gatekeeper.
A deceleration device that travels on a lifeline and automatically engages the lifeline and locks so as to arrest a fall. ANSI/ ASSP refers to them as fall arresters.
A deceleration device containing a drum-wound line which can be slowly extracted from, or retracted onto, the drum under slight tension during normal worker movement. After onset of a fall, the unit automatically locks the drum and arrests the fall within 2 feet. ANSI/ASSP standards use the term self-retracting device (SRD) to refer to all types of SRLs.
A self-closing device with a keeper, latch, or other similar arrangement that will remain closed until manually opened. Snap hooks used in personal fall protection should be self-closing and self-locking and only be capable of opening with at least two consecutive actions by the user.
A length of webbing that provides a strength member that may be incorporated in a harness, lanyard, or other component or subsystem.
A full-body harness strap, which passes under the buttocks without passing through the crotch, which is designed to transmit forces applied during fall arrest or post-fall suspension to the sub-pelvic part of the body.
A condition that may occur when a person falls and remains suspended both vertical and sedentary for a period of time. Blood pools in the veins of the legs, which could result in unconsciousness. If a person is not rescued quickly, permanent damage and possibly death may result.
A pendulum-like motion that can result from a fall after moving horizontally away from a fixed anchorage.
A flexible line of heavy-duty, abrasion-resistant webbing designed to be used as the connecting device and anchorage connector with a specially engineered snap hook able to withstand 5,000 lb. (22 kN) on the body and gate.
Solutions that are applied to tools being used at height to create secure connection points for tool tethers and that which are not integral to that tool.
A length of material with at least one connector on each end that will connect a tool to an anchor.
The maximum vertical distance between a full body harness attachment point and the lowest extremity of the body before and after the fall is arrested including lanyard extension and/or deceleration distance.
A fall arrester which moves freely up and down the lifeline with handsfree operation.
A component, element, or constituent of a lifeline subsystem which consists of a vertically suspended flexible line and connector for fastening it to an overhead anchorage, or anchorage connector, and along which a fall arrester travels.
Regulations and Standards
OSHA Regulations Title 29 of the Code of Federal Regulations
OSHA published a revision to the walking-working surfaces standards in 2016 and added a fall protection section to the personal protective equipment standards for general industry. Text of these regulations can be found on the OSHA website.
Occupational Safety and Health Standards for General Industry
Subpart D, Walking-Working Surfaces
- Scaffolds and Rope Descent Systems: 1910.27
- Duty to have Fall Protection and Falling Object Protection: 1910.28
- Fall Protection Systems and Falling Object Protection—Criteria and Practices: 1910.29
- Training Requirements: 1910.30
Subpart F, Powered Platforms, Man lifts, and Vehicle-Mounted Work Platforms
- Powered Platforms for Building Maintenance: 1910.66
- Vehicle-mounted elevating and rotating work platforms: 1910.67(c)(2)(v)
Subpart I, Personal Protective Equipment
- Personal Fall Protection Systems: 1910.140
- Scope and Application: 1910.140(a)
- Definition: 1910.140(b)
- General Requirements: 1910.140(c)
- Personal Fall Arrest Systems—Performance and Use Criteria: 1910.140(d)
- Positioning Systems— Performance and Use Criteria: 1910.140(e)
- PFAS Non-Mandatory Guidelines: Appendix C
- Test Methods and Procedures for PFAS Non-Mandatory Guidelines: Appendix D
Subpart J, Permit-Required Confined Space: 1910.146
Subpart R, Special Industries
- Pulp, Paper, and Paperboard Mills: 1910.261(g)(2)(ii)
- Telecommunications: 1910.268(g)
- Electric Power Generation, Transmission, and Distribution: 1910.269(g)(2)
Safety and Health Standards for Construction
Subpart E, Personal Protective and Life Saving Equipment
- Safety Belts, Lifelines, and Lanyards: 1926.104
- Safety Nets: 1926.105
Subpart L, Scaffolding
- Fall Protection: 1926.451(g)
Subpart M, Fall Protection
- Scope, Application, and Definitions: 1926.500
- Duty to have Fall Protection: 1926.501
- Fall Protection Systems Criteria and Practices: 1926.502
- Training Requirements: 1926.503
- PFAS—Non-Mandatory Guidelines: Appendix C
- Positioning Device Systems—Non-Mandatory Guidelines: Appendix D
- Sample Fall Protection Plan—Non-Mandatory Guidelines: Appendix E
Subpart R, Steel Erection
- Falling Object Protection: 1926.759
- Fall Protection: 1926.760
Subpart V, Electric Power Transmission and Distribution
- Personal Fall Arrest Systems: 1926.954(b)(1)
- Work-Positioning Equipment: 1910.954(b)(2)
- Care and Use of Personal Fall Protection Equipment: 1910.954(b)(3)
Subpart X, Stairways and Ladders
- Ladders: 1926.1053
Safety and Health Standards for Shipyard Employment, Marine Terminals, and Longshoring
- Shipyard Employment: Personal Fall Arrest Systems: 1915.159
- Shipyard Employment: Positioning Device Systems: 1915.160
- Marine Terminals: Employee Protection (Guardrails): 1917.112(b)
- Longshoring: Fall Protection: 1918.85(j) & (k)
Relevant Consensus Standards
American National Standards
This list represents active standards at the time this document was published. Standards change and are updated frequently. Refer to
the most current version of standards for more information.
ANSI/ASSP Z359 Standards
- Z359 Committee Guidance Document for Definitions and Nomenclature Used in Z359 Fall Protection and Restraint Standards:
Z359.0 - The Fall Protection Code: Z359.1
- Minimum Requirements for a Comprehensive Managed Fall Protection Program: Z359.2
- Safety Requirements for Lanyards and Positioning Lanyards: Z359.3
- Safety Requirements for Assisted Rescue and Self-Rescue Systems, Subsystems and Components: Z359.4
- Specifications and Design Requirements for Active Fall Protection Systems: Z359.6
- Qualification and Verification Testing of Fall Protection Products: Z359.7
- Safety Requirements for Full Body Harnesses: Z359.11
- Connecting Components for Personal Fall Arrest Systems: Z359.12
- Personal Energy Absorbers and Energy-Absorbing Lanyards: Z359.13
- Safety Requirements for Self-Retracting Devices for Personal Fall Arrest and Rescue Systems: Z359.14
- Safety Requirements for Single Anchor Vertical Lifelines and Fall Arresters for Personal Fall Arrest Systems: Z359.15
- Safety Requirements for Climbing Ladder Fall Arrest Systems: Z359.16
- Safety Requirements for Anchorage Connectors for Active Fall Protection Systems: Z359.18
Personal Fall Protection Used in Construction and Demolition Operations: ANSI/ASSP A10.32
Ladders – Fixed – Safety Requirements: ANSI ASC A14.3
Safety Requirements for Entering Confined Spaces: ANSI/ASSP Z117.1
Standard Specifications for Personal Climbing Equipment: ASTM F887
The U.S. Army Corps of Engineers
The USACE has its own safety and health requirements that apply to all Corps of Engineers activities and operations. EM 385-1-1 is
the Safety and Health Requirements Manual where all these requirements are laid out. “EM” stands for “Engineering Manual.”
CAN/CSA Canadian Standards
- Body Belts and Saddles for Work Positioning and Travel Restraint: Z259.1
- Self-Retracting Devices: Z259.2.2
- Descent Devices: Z259.2.3
- Fall Arresters and Vertical Rigid Rails: Z259.2.4
- Fall Arresters and Vertical Lifelines: Z259.2.5
- Full Body Harnesses: Z259.10
- Personal Energy Absorbers and Lanyards: Z259.11
- Connecting Components for Personal Fall Arrest Systems (PFAS): Z259.12
- Manufactured Horizontal Lifeline Systems: Z259.13
- Fall Restrict Equipment for Wood Pole Climbing: Z259.14
- Anchorage Connectors: Z259.15
- Design of Active Fall-Protection Systems: Z259.16
- Selection and Use of Active Fall-Protection Equipment and Systems: Z259.17
Global Fall Protection Standards
Fall protection standards and regulations in countries outside of North America are beyond the scope of this document. The following links provide access to information on fall protection standards in other parts of the world.
European Standards and Regulation
Fall protection is covered under the European PPE Directive, which imposes uniform requirements and consistent approval for all European countries. Fall protection equipment in Europe bears the “CE” mark to show compliance with the directive. More information can be found here.
European standards for fall protection come under the purview of Technical Committee 160 of the European Committee for Standardization (CEN). A listing of those standards can be found here.
European standards are accepted as national standards and sold through national standards’ bodies. English language editions can be found at the ANSI webstore by adding the prefix “BS” in front of the EN standard number in the search box, or going to the BSI webstore.
ISO Standards
The ISO committee for fall protection (TC94 SC4) is currently inactive, and the U.S. is not a participating member. Some of the ISO standards have been adopted as national standards, but their use is not widespread.
China Standards
China National Standards (GB) are mandatory requirements for products and services. GB standards for fall protection equipment can be purchased online. Go to https://www.gbstandards.org/ and enter “fall protection” in the search box.
Other Global Standards
Many countries have standards for fall protection equipment that can be found on sites providing engineering documents. Search for standards using keywords such as “fall protection” or “rope access” using the standards’ developer abbreviations:
- Australia/New Zealand: AS/NZS
- Brazil: NBR
- Japan: JSA
- Korea: KSA
- Russia: GOST
- South Africa: SABS
Searchable directories of fall protection standards can be found at:
- SAI Global, a subsidiary of Standards Australia.
- ANSI Webstore, from the American National Standards Institute.
Also check manufacturers’ websites for links to global standards.
ISEA Fall Protection Manufacturers
The following companies are members of the ISEA Fall Protection Group. For information on fall protection products and systems from ISEA members, check the online Buyers Guide.
- 3M
- 3m.com/ppe
- Buckingham Manufacturing Co.
- buckinghammfg.com
- DeltaPlus Group
- deltaplus.eu
- DFP Safety
- dfpsafety.com
- Ergodyne
- ergodyne.com
- FallTech
- www.falltech.com
- Guardian Fall
- guardianfall.com
- Honeywell
- ppe.honeywell.com
- Ironwear
- ironwear.com
- Klein Tools, Inc.
- kleintools.com
- MSA Safety
- msasafety.com
- Petzl
- petzl.com
- SafeWaze
- safewaze.com
- SureWerx
- surewerx.com
- Werner Cobuckinghammfg.com
- wernerco.com
For More Information
U.S. Occupational Safety and Health Administration (OSHA)
200 Constitution Avenue, NW
Washington, DC 20210
www.osha.gov
The OSHA website has access to fall protection regulations, directives and interpretations, plus compliance aids and other information. A good place to start is the Fall Protection Safety and Health Topics page at Safety Management – A safe workplace is sound business | Occupational Safety and Health Administration (osha.gov) and their supplied fact sheets Occupational Safety and Health Administration (osha.gov). Note: Some of the standards and regulatory information on this site may be out of date.
For information on voluntary standards, contact:
American National Standards Institute (ANSI)
25 West 43rd Street
New York, NY 10036
Phone: (212) 642-4900
www.ansi.org
Do not call ANSI to ask about a specific standard. Questions and requests for interpretation must be directed to the standards developing organization.
For fall protection standards (A10.32, Z117, Z359) the secretariat is:
American Society of Safety Professionals (ASSP)
520 N. Northwest Highway,
Park Ridge, IL 60068, USA
Phone: (847) 699-2929
www.assp.org
International Safety Equipment Association (ISEA)
1101 Wilson Boulevard, Suite 1425
Arlington, VA 22209
Phone: (703) 525-1695
www.safetyequipment.org
ISEA is the trade association for personal protective equipment and technologies.
For questions about Canadian standards, contact:
CSA Group
178 Rexdale Boulevard,
Toronto, Ontario M9W 1R3, CA
Phone: (800) 463-6727
www.csagroup.org