Application Solutions
Portable Gas Detection
Today’s gas monitoring equipment has come a long way over the past 50 years. Gas detection sensor technology safety advancements offer dramatic reductions in size and cost of personal multi-gas monitors, allowing employers to protect more workers against potential hazardous gas exposure.
Gas detector manufacturers have invested considerable research and resources in the development of small, personal multi-gas monitors to be worn comfortably as part of worker personal protective equipment (PPE). Wider acceptance by workers of these detectors translates to a higher level of protection against potential hazards presented by toxic gases, oxygen-deficient and enriched environments and potentially explosive atmospheres in the presence of combustible gases.
Working in a Confined Space
A critically important application for multi-gas monitors in many industrial settings is confined space entry. Recognition of confined space entry potential hazards is fundamental in avoiding fatalities. Worker fatalities associated with confined spaces are recurring occupational tragedies. According to NIOSH (National Institute for Occupational Safety and Health), approximately 60% of deaths involve would-be rescuers. With the proper equipment and training, most of these fatalities can be prevented. When working within confined spaces, atmospheric monitoring is vital. Multi-gas monitors have a variety of applications across all industries for ambient air monitoring beyond confined personal space monitoring.
A confined space is any space large enough for an employee to enter and perform work. A confined space has limited means of entry or exit and is not designed for continuous occupancy. A permit required confined space has one or more of the following characteristics:
- A hazardous atmosphere (oxygen deficiency, toxic gases or explosive gases) is present or has the potential to be present.
- Material with potential for engulfment is present.
- The space has inwardly sloping walls or dangerously sloping floors.
- The space has any other serious safety hazard.
The Occupational Safety and Health Administration (OSHA) put the Permit Required Confined Spaces Final Rule (29 CFR 1910.146) into effect on April 15, 1993. OSHA also specifies requirements of non-permit required confined space. Procedures for atmospheric testing can be found on OSHA’s Web site at www.osha.gov.
Confident in Your Portable Gas Detection Know-How?
Take our short quiz to see how well you really understand the tools, techniques, and technologies that keep workers safe.
Docking Your Monitors
Portable gas detection docking stations are increasingly popular among employers and safety managers. Here’s why: These systems automatically conduct functional tests and calibrations, record data and charge monitors, allowing the next crew to grab their monitors and go to work. If proof of proper maintenance and care of gas detectors must be given, docking stations provide objective evidence that procedures were followed. Software integration provides safety managers with status reports and other information necessary to achieve a complete instrument management system.
Using this Guide
This guide’s purpose is to aid new users of portable gas detection with a basic understanding of available detection technologies. In this guide are examples of both single-gas and multi-gas options to provide overall hazardous gas detection coverage, including pros and cons of each depending on the application. Your facility’s gas detection requirements should always, be determined by a qualified safety professional.
NOTE: This guide is provided for informational purposes only and should not be used as a substitute for professional advice. The content is not guaranteed to be accurate, complete, reliable, current or error-free. By accessing this document, you accept and agree that following any information provided therein is at your own risk.
Looking for details about fixed systems?
Fixed Systems for your Flame and Gas Detection Application Solutions is available to assist users of fixed gas detection systems with basic understanding of available detection technologies.
Sensor Technologies
Catalytic Bead Sensors
Catalytic Bead Sensors, also known as pellistors, oxidize combustible gas. A heated, catalyst-coated coiled wire burns (catalyzes) the gas of interest; the wire temperature increases along with its electrical resistance. Wheatstone Bridge circuitry employs two detectors, one for detection and one for compensation. The first detector converts the resistance change into a corresponding, measurable signal. The second detector compensates for temperature, pressure and humidity. Gas readings display as percent LEL (Lower Explosive Limit).
- Pros: long life, less sensitive to temperature, humidity, condensation, and pressure changes (as compared to NDIR), high accuracy, fast response, monitors a wide range of combustible gases and vapors in air.
- Cons: subject to sensor poisoning, requires air or oxygen, shortened life with frequent or continuous exposure to high LELs, non-specific detection, higher power draw, inability to detect failure in between bumps, inability to measure above LEL.
Metal Oxide Semiconductor Sensors
Metal Oxide Semiconductor Sensors, also known as solid state sensors, detect combustible and toxic gases. Metal oxide sensors, through use of electrodes, changes resistance in response to gas presence. Resistance change is measured and is proportional to the gas concentration of interest. Gas reading displays as ppm (parts per million).
- Pros: high sensitivity (detects low concentrations), wide operating temperature range, long life.
- Cons: cross-sensitive to other compounds, humidity-sensitive, subject to poisoning, requires air/oxygen for proper function.
Infrared Sensors
Infrared Sensors (AKA non-dispersive infrared or NDIR) measure hydrocarbon gases (i.e. methane, ethane, propane) or carbon dioxide dependent upon the wavelength. Detectors are sensitive to varied infrared wavelength ranges. The gas of interest and inert reference gas are exposed to infrared light; amount of light transmitted through each sample (the O2 is not necessary; measures the number of hydrocarbon molecules present) is compared to determine gas of interest concentration. A microprocessor monitors signals ratio and correlates results to a readable signal (the units of measure in % LEL or % Vol and consider linearization of the reading based upon the signal ratio).
- Pros: high accuracy, calibration frequency, and selectivity, large measurement range, low maintenance, resistant to chemical poisoning requires no oxygen, long operating life (as compared with catalytic bead).
- Cons: unsuitable for hydrogen and acetylene detection.
Electrochemical Gas Sensors
Electrochemical Gas Sensors (e-chem) use an electrolyte and active electrodes to produce an electrochemical reaction to generate current proportional to the present target gas concentration. Gas reading display EC sensor could be ppm or % Vol (O2).
- Pros: high sensitivity, low power consumption.
- Cons: limited shelf life, sensor lifetime is reduced when used in very dry, hot environments, can be affected by interferents, requires oxygen (all ECs need O2) certain electrochemical sensors require stabilization period.
Electrochemical Sensor
Electrochemical Sensor with oxygen deficiency and enrichment with consumable anode use an electrolyte and electrodes to produce an electrochemical reaction to generate a current proportional to the gas concentration. Gas reading displays as percent by (%Vol).
- Pros: high sensitivity, low power consumption.
- Cons: limited shelf life, sensor lifetime is reduced when used in very dry, hot environments within enriched oxygen environments, or complete lack of oxygen. Lead-based sensors are subject to environmental disposal issues.
Long Life Electrochemical Sensors
Long Life Electrochemical Sensors for oxygen deficiency and enrichment. This oxygen pump is designed to be maintenance-free and stable for long periods. It uses technology from both the original oxygen and toxic gas sensors which results in a direct response to volume concentration rather than partial pressure. A feature of the design is the capillary diffusion barrier, which limits the access of gas to the sensing electrode. The electrode is therefore able to react to all target gas as it reaches its surface and still has electrochemical activity in reserve.
- Pros: high sensitivity, ease of handling, low power consumption. The high activity reserve ensures each has a long life of up to 5 years and excellent temperature stability.
- Cons: A period of stabilization time will be required before meaningful measurements can be taken.
Paper Tape Technology
Paper Tape Technology is based upon the use of absorbent filter paper strips that act as a dry reaction substrate. Classic colorimetry techniques used are capable of extremely low toxic gas detection limits.
- Pros: highly sensitive and selective for toxic gases. Leaves physical evidence of gas exposure. No false alarms.
- Cons: requires extraction system. May need sample conditioning. High maintenance.
Thermal Conductivity Sensors
Thermal conductivity sensors for combustible and toxic gases measure the gas sample’s heat transmitting ability by comparing it with a reference gas (usually air). Detectors, electrodes, or MEMS surfaces create an electrical output in response to thermal characteristics of the analyte. Responses are analyzed and compared to a baseline reference to produce a gas reading. Gas reading displays as parts per million up to 100% VOL.
- Pros: wide measuring range, low power, and limited poison potential.
- Cons: cross-sensitive to other compounds), ineffective for measuring gases with certain thermal conductivities (close to air). Ineffective when analyte background significantly changes from calibration background gas (inerting).
Photo Ionization Detectors Sensors (PIDs)
Photo Ionization Detectors Sensors (PIDs) use ionization to detect volatile organic compounds (VOCs). Ultraviolet lamp within sensor ionizes the compound of interest. Collected ions and the corresponding current produce a readable concentration of the compound of interest. Gas reading displays as parts per million (ppm) and parts per billion (ppb).
- Pros: fast response speed, very low-level detection, detects many compounds
- Cons: high maintenance, limited operating life, requires frequent calibration, humidity-sensitive responses to many VOCs with ionization potentials below the electron volt rating of the lamp, Inability to detect gases with ionization energies above lamp power.
Flame Ionization Detectors (FIDs)
Flame Ionization Detectors (FIDs) are generally used to detect organic compounds. Compounds of interest are ionized using a small hydrogen flame generated within the detector. The resulting charged ions create current between electrodes; this measurable current is used to determine the proportion of carbon that has been reduced by flame exposure. Gas reading displays in picograms.
- Pros: high sensitivity, ease of use.
- Cons: high maintenance sensor, requires presence of hydrogen and air, gas sample is destroyed by FID process.
Acronym Key:
- LEL Lower Explosive Limit (combustible gases)
- Ppm Parts Per Million (toxic & VOC)
- Ppb Parts Per Billion
- %Vol Percent by Volume (oxygen)
- VOC Volatile Organic Compounds (PID)
- PID Photo Ionization Detection (VOC)
- TWA Time Weighted Average (toxic gases)
- STEL Short Term Exposure Limit IP Ionization Potential & Ingress Protection
- IS Intrinsic Safety Rating (UL, CSA)
- T90 Time sensor needs to reach 90% full response
- IDLH Immediately Dangerous to Life and Health
- PEL Permissible Exposure Limit (set by OSHA)
Portable Gas Detection Applications
Oil, gas, petrochemical refineries, chemical plants
- E-chem toxic gas leak detection, oxygen within confined spaces
- E-chem for oxygen deficiency for confined space entry
- Catalytic bead and NDIR for combustible gas detection
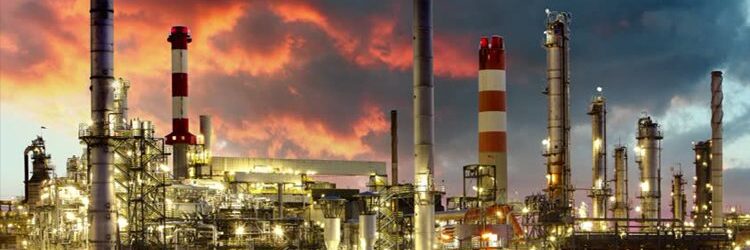
General confined space entry
- E-chem for toxic gas, oxygen detection within confined spaces
- Catalytic bead and NDIR for combustible gas detection
- E-chem and NDIR (CO2) toxic gas leak detection, oxygen within confined spaces
- PID for volatile organic compounds
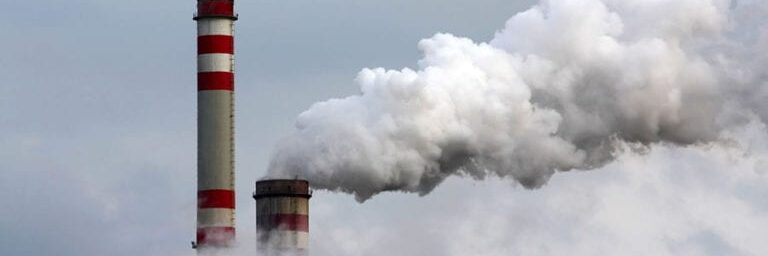
Municipal water, wastewater treatment facilities
- UV/IR for hydrocarbon-based fires
- E-chem for chlorine, sulfur dioxide, hydrogen sulfide, oxygen as water treatment by-products
- Point IR, catalytic bead for combustible methane and petroleum vapors within wet well areas
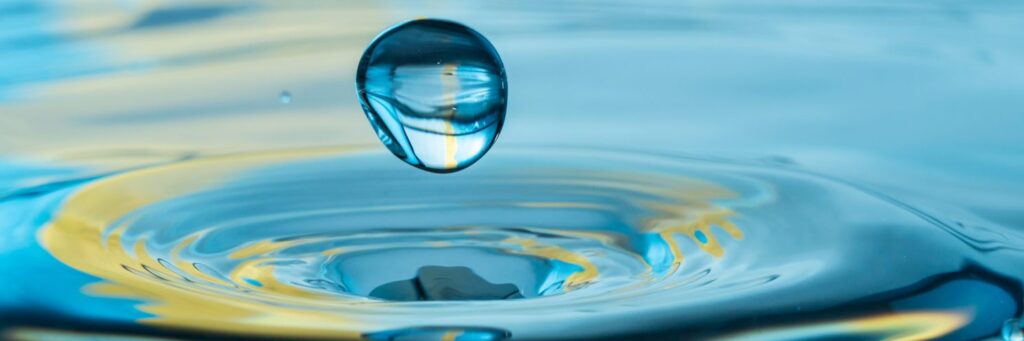
HVAC
- Catalytic bead and NDIR for refrigerants, cleaning agents and solvents in mechanical
equipment rooms - Â E-chem for carbon monoxide and nitrogen dioxide in parking garages, tunnels, furnace,
and maintenance rooms - Â NDIR, MOS and e-chem for carbon monoxide, nitrogen dioxide, refrigerants
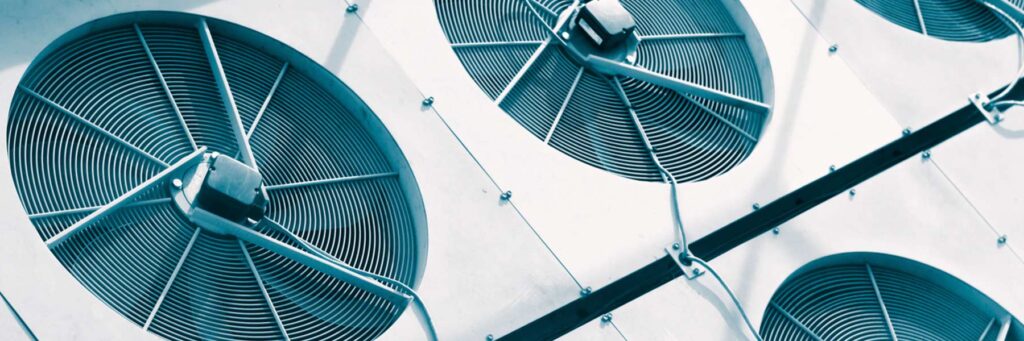
Hospitals/other medical facilities
- E-chem for ethylene oxide leaks within laboratories, surgical areas, ICUs
- E-chem for refrigerant gas leaks in mechanical chiller rooms
- Â Catalytic bead for hydrogen detection
- Â E-chem for oxygen deficiency within MRI rooms
- Â E-chem for nitrous oxide leaks within cylinder storage areas
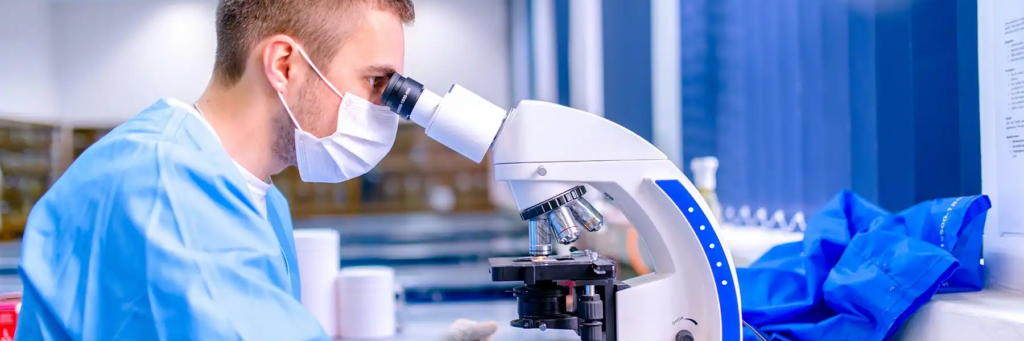
Iron and steel
- Â E-chem for toxic gases or oxygen deficiency; catalytic bead for combustible and toxic gases, potential oxygen deficiency in blast furnace operation maintenance, converter operation, furnace/gas pipeline leaks, metal mining, finishing work, fuel storage, coking operations, welding, confined space
- Â NDIR point IR for refrigerant gases used in maintenance rooms (chillers)
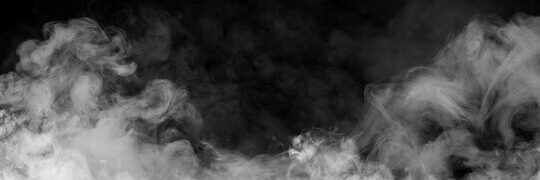
Airports
- Â Catalytic bead, NDIR, PIR for combustible and toxic gases in fuel storage/fuel loading areas, pump
houses, storage hangars - Point IR, e-chem for carbon monoxide/nitrogen dioxide buildup within baggage handling areas,
parking garages - IMS for explosive residue screening
- UV, UVIR for flame detection within hangars and storage areas
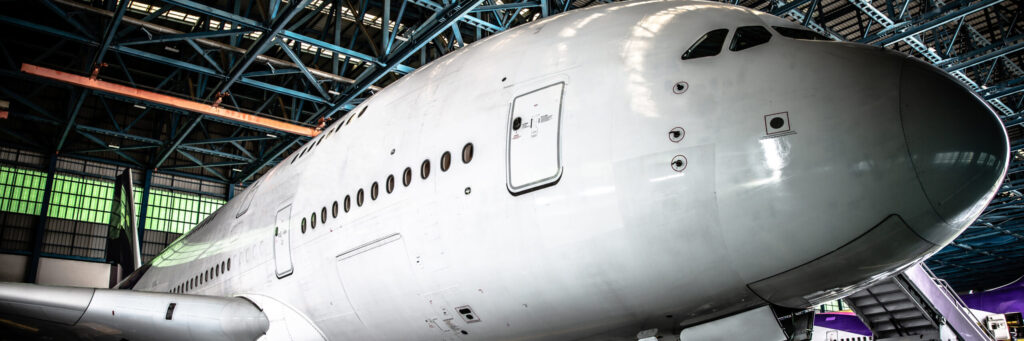
Mining
- NDIR for combustible gases within confined space, mechanized coal cutting, diesel-powered machinery exhaust
- E-chem (oxygen) for confined space entry, toxic gases in metal mining, diesel exhaust, dieselpowered machinery, blasting
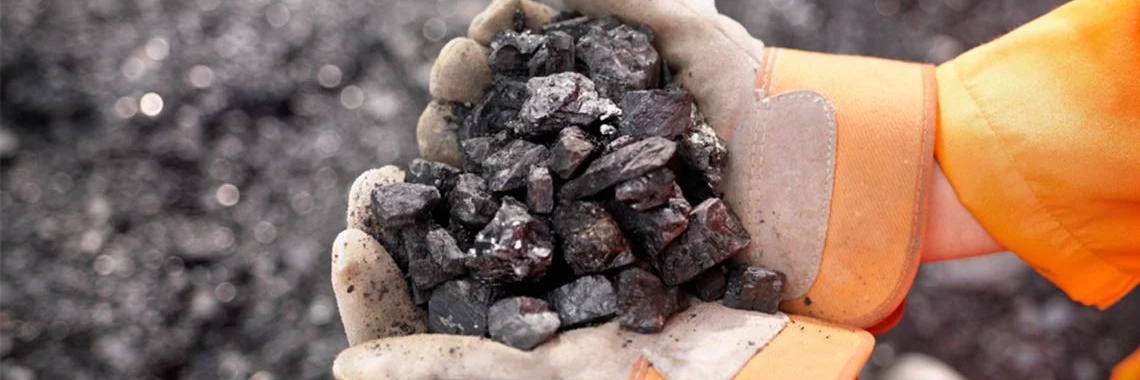
Wireless Connectivity in Portable Gas Detection
Wireless connectivity has seamlessly woven itself into various aspects of our daily lives, its influence on portable gas detectors also has not gone unnoticed. Manufacturers of modern detectors have embraced connectivity options such as RFID readers, Bluetooth, Wi-Fi, and integrated cellular, providing users with a multitude of benefits aimed at enhancing their safety and efficiency, including:
Greater Situational Awareness
One of the primary benefits of incorporating wireless connectivity into portable gas detectors is the immediate enhancement of situational awareness. Real-time monitoring on mobile devices and computers empowers users with critical information, including exposure alarms, low-battery warnings, and man-down alerts. These vital notifications can be swiftly communicated to designated monitoring individuals or other workers, improving outcomes in response to potential hazards.
Simplified Compliance
Wireless connectivity streamlines compliance-related tasks, offering users better visibility into the condition of their detectors. Users can easily identify which detectors are due for calibration, track those that require daily bump tests, and access data logs conveniently. This simplification of compliance procedures not only ensures safety but also reduces the administrative burden associated with gas detector maintenance.
Reduced Cost of Ownership and Operation
Enhanced visibility into the maintenance needs of detectors translates into a reduced cost of ownership and operation. By promptly identifying detectors requiring attention, users can schedule maintenance more efficiently, minimizing downtime. Manufacturers are also embracing over-the-air firmware updates, eliminating the need for a hands-on approach that was prevalent in the past. This innovation further contributes to cost savings and ensures that detectors remain up to date with the latest improvements.
Streamlined Setup and Configuration
Wireless connectivity eliminates the limitations of traditional button and screen interfaces, making setup and configuration of detectors more intuitive and user-friendly. Users can conveniently configure their devices using computers or mobile devices, streamlining the process and reducing the potential for errors during setup.
Many other value-added benefits will continue to be realized as manufacturers evolve their cloud software services and leverage data to help portable gas detector users improve their gas detector programs.
This guide was developed with the help of the following ISEA members:
- 3M
- 3m.com
- DRAEGER
- draeger.com
- HONEYWELL
- honeywell.com
- INTERTEK
- intertek.com
- MSA SAFETY
- msasafety.com